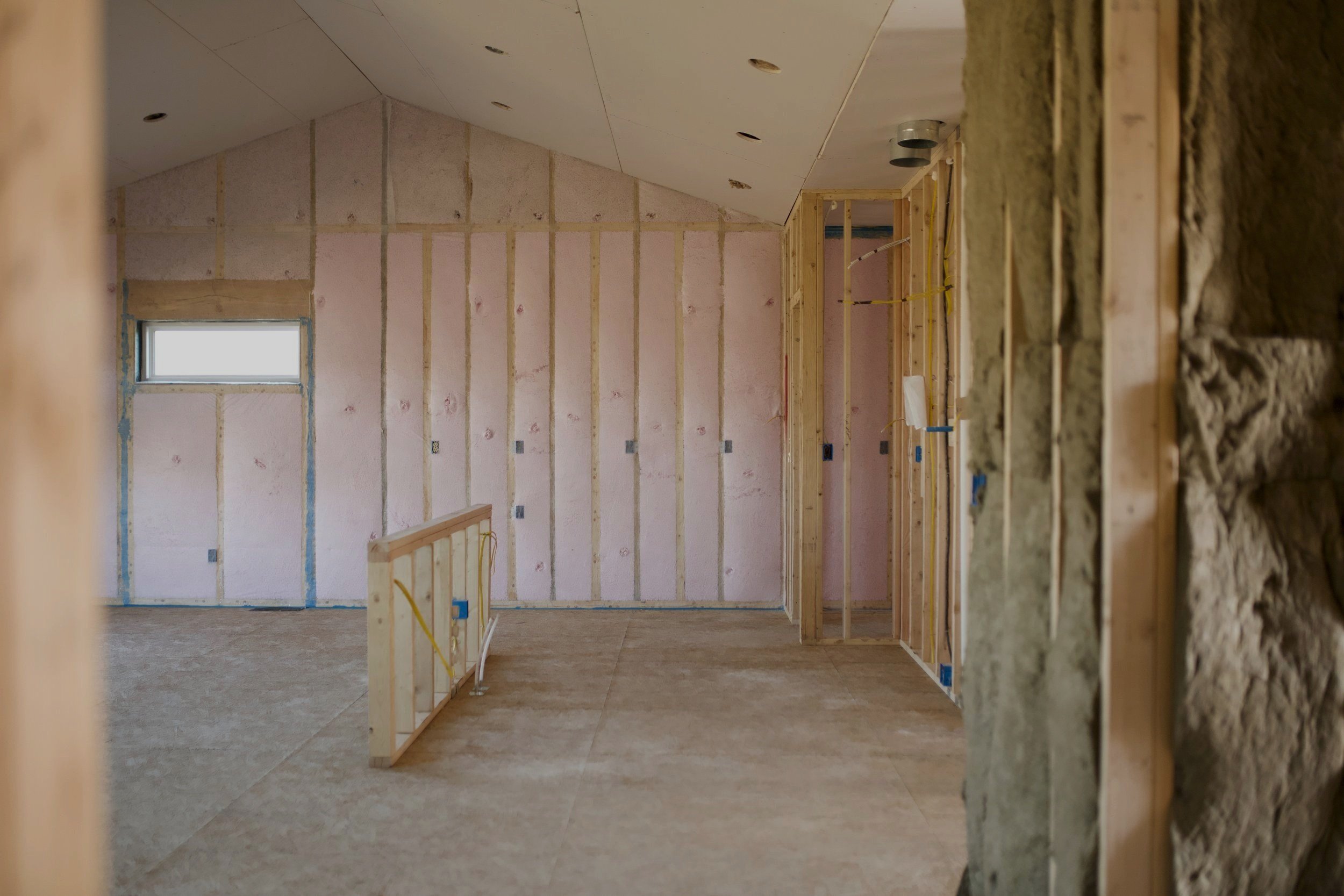
Timber Creek
Timber Creek is the personal residence of Thermal Shop’s founder and president,
Jacob Heffernen.
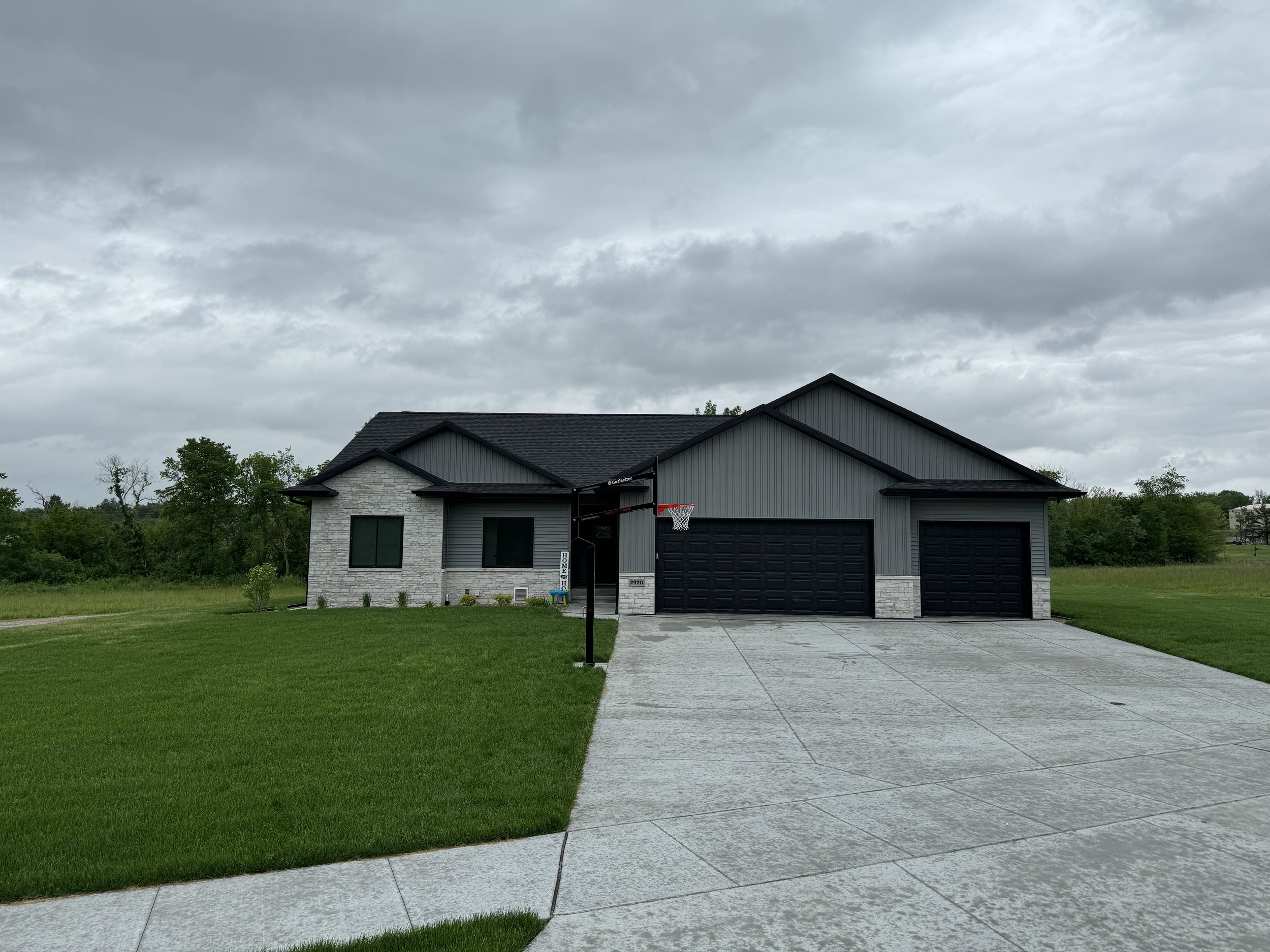
Timber Creek was designed with several different goals in mind.
First- build a comfortable house. A house that maintains a consistent air and surface temperature despite seasonal fluctuations; one that feels the same year-round.
Second- build an efficient house. Luckily for homeowners, efficiency oftentimes comes as a byproduct of comfortability.
Third- build a beautiful and functional house that suits family needs.
In the end, Timber Creek is truly a house fit for the President of an insulation company. It is an extremely comfortable and efficient house. It is tightly air-sealed, and has superior thermal and sound insulation.
Jump to Section
| Concrete Slab | T-Studs | Exterior Shell | EcoSeal | Windows | Spray Foam | Net & Blow | Sound Insulation | Hybrid Insulation | Attic | Garage | Energy Testing |
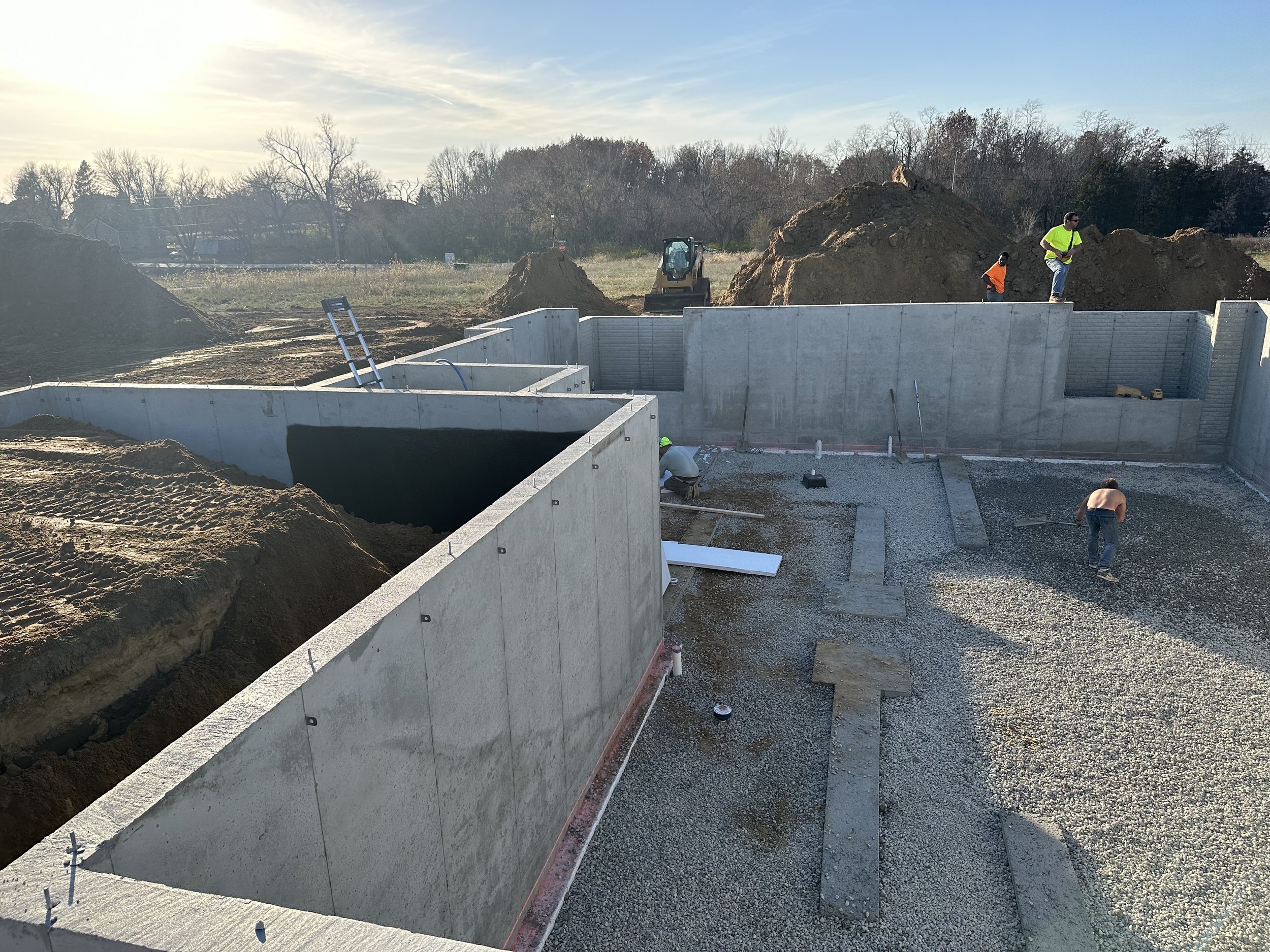
Concrete Slab
To improve the thermal barrier underneath the house, Thermal Shop started by installing 2” of foam board sealed with tape at the seams.
The foam board was then topped with 15 millimeter poly sheeting, and covered it all with a 4” concrete slab.
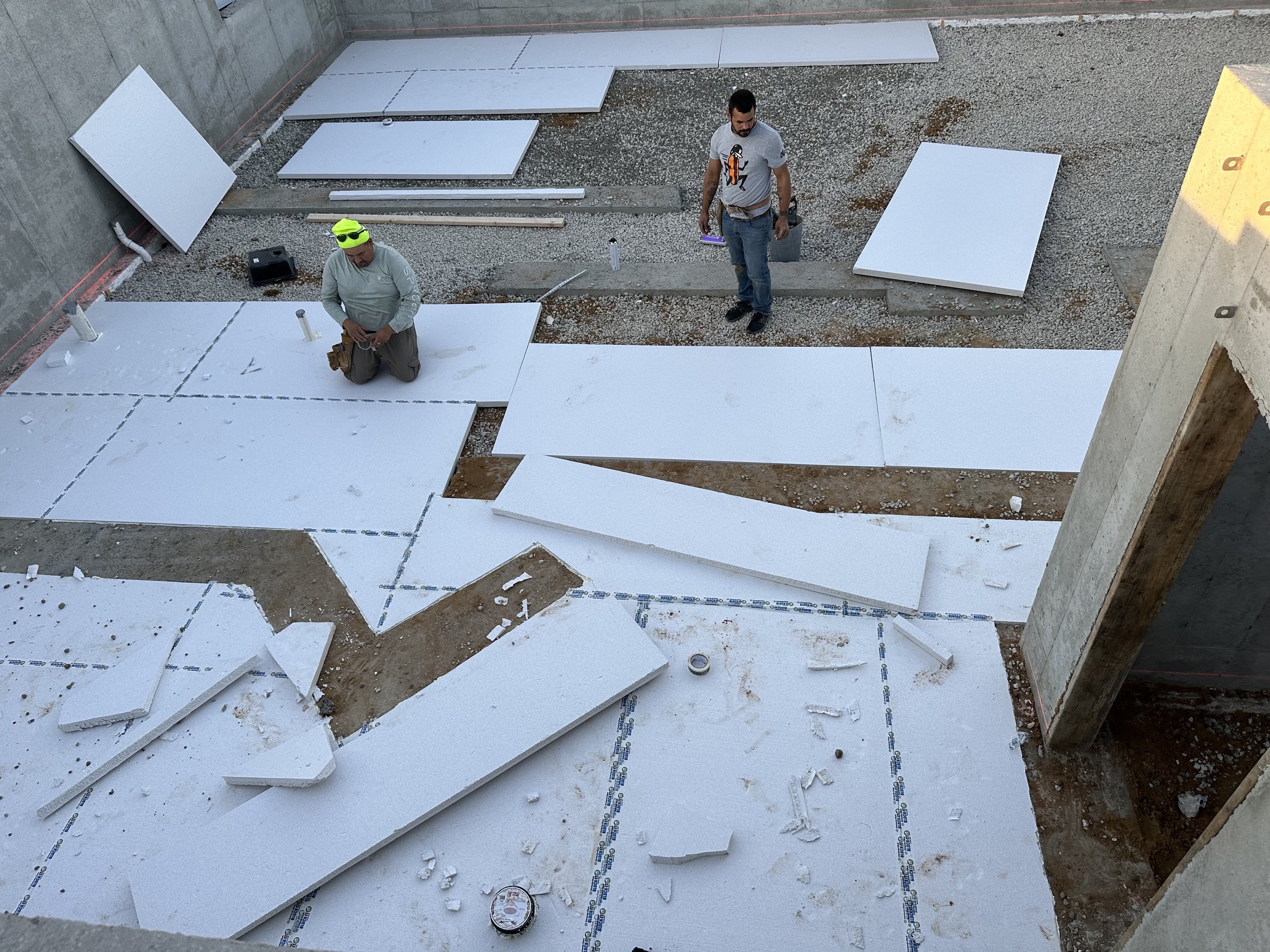
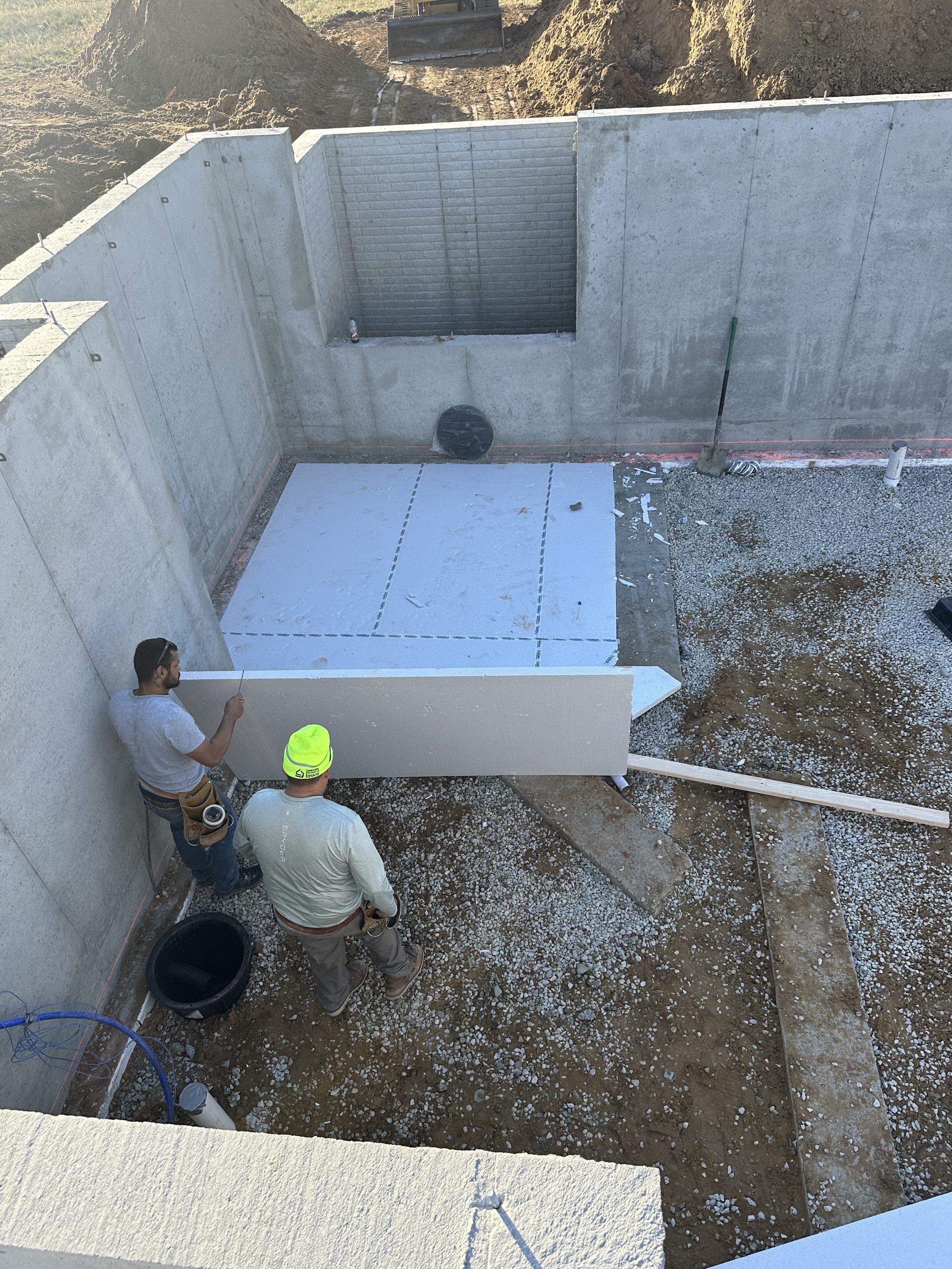
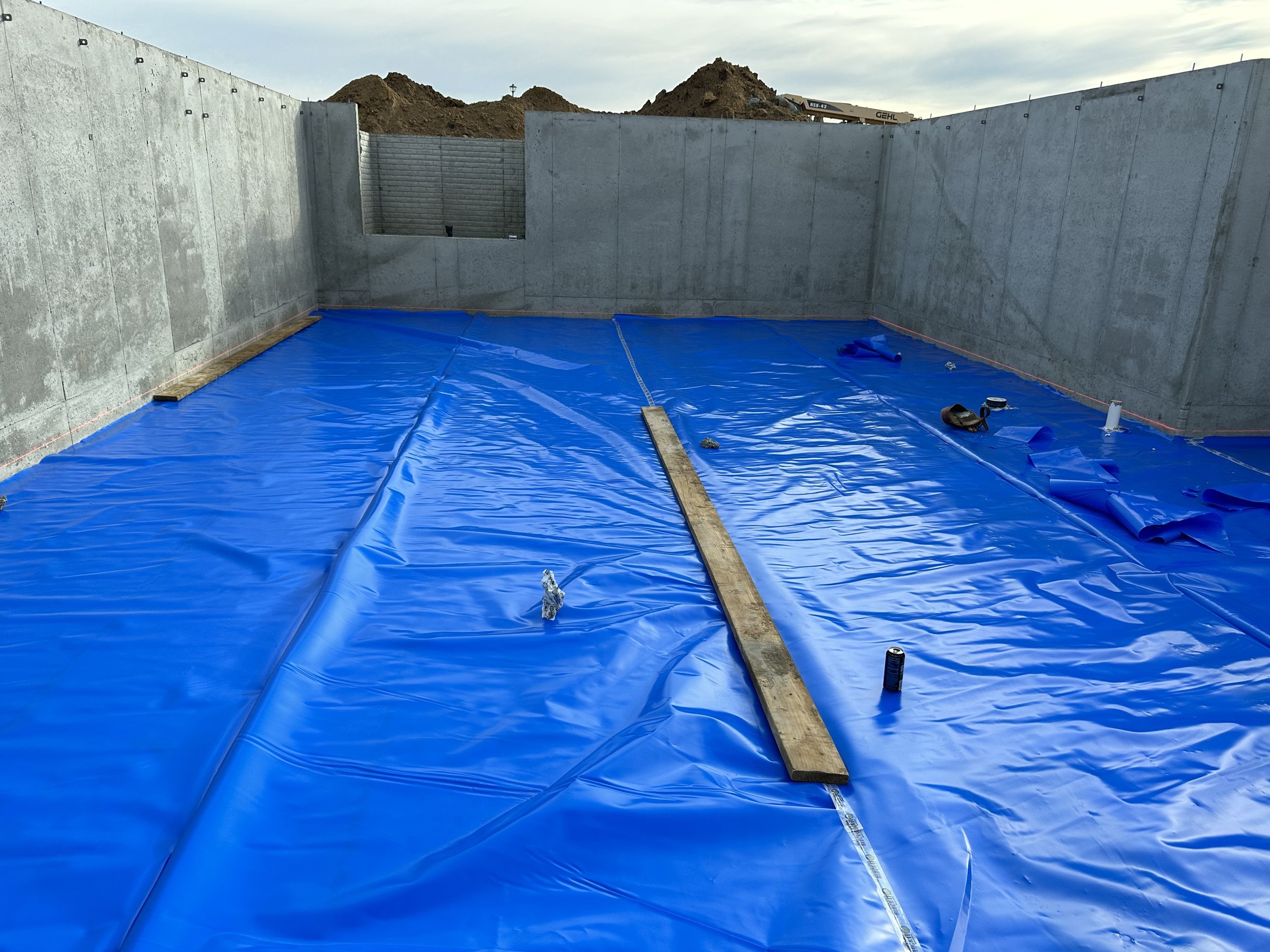
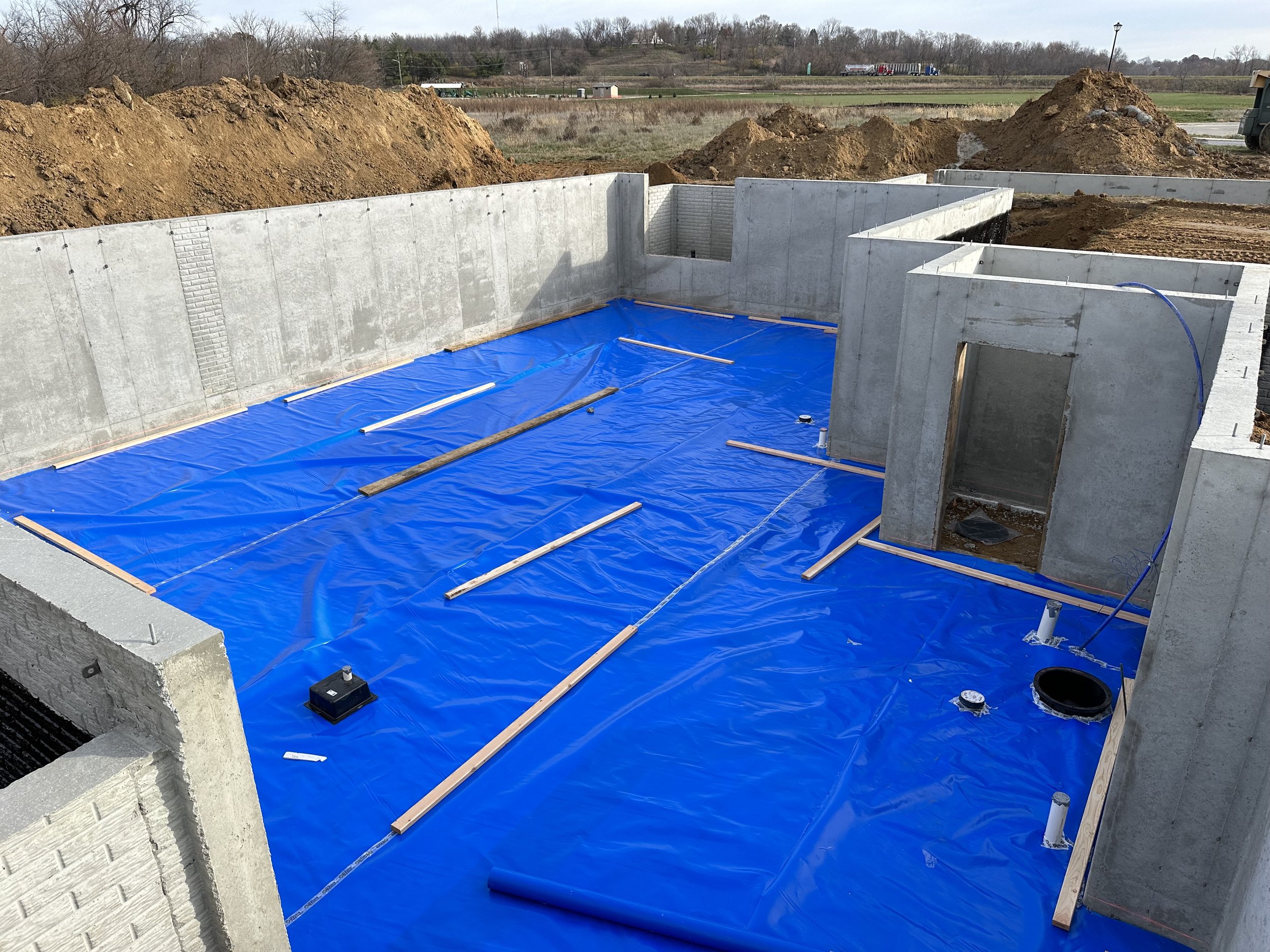
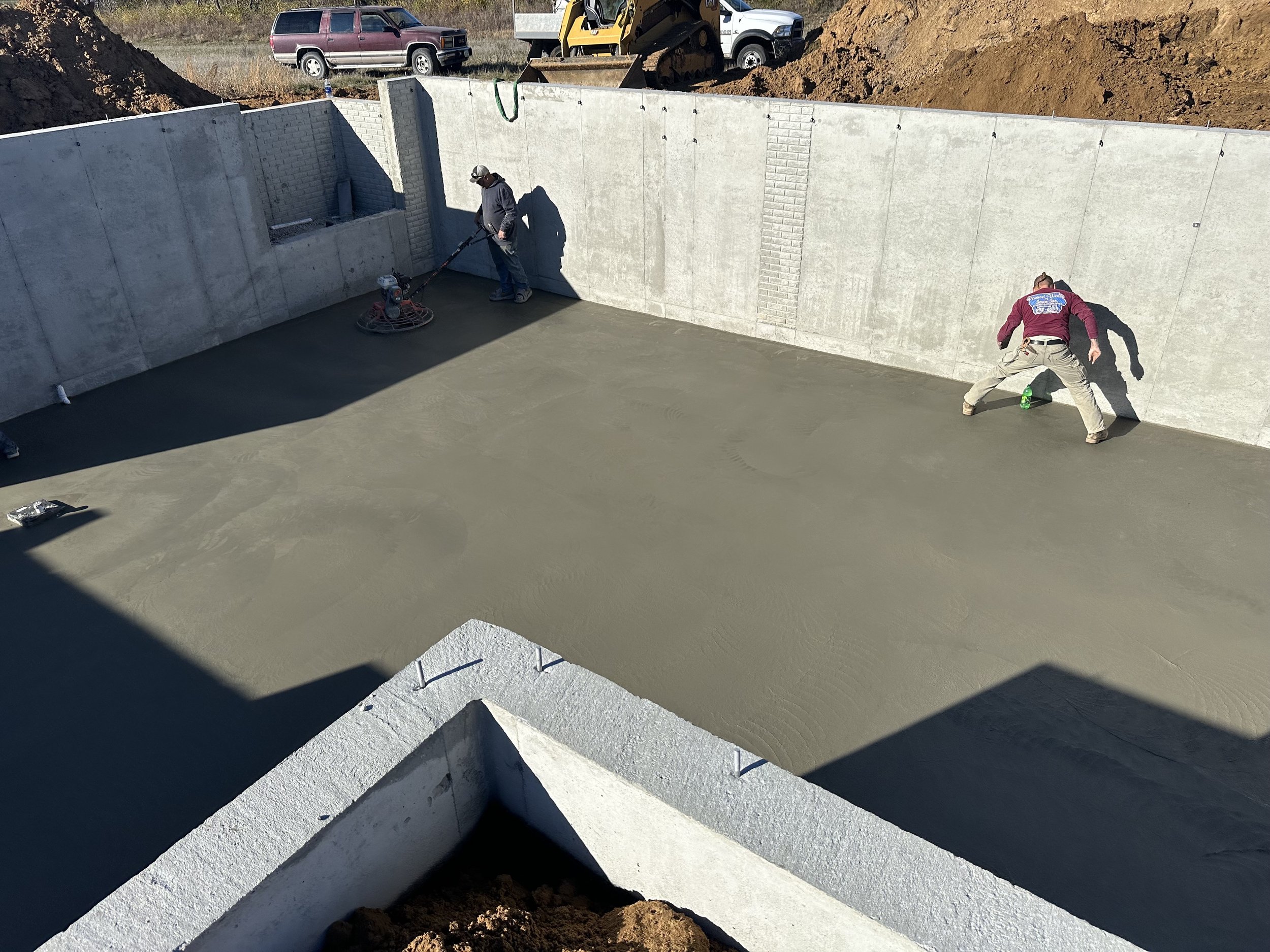
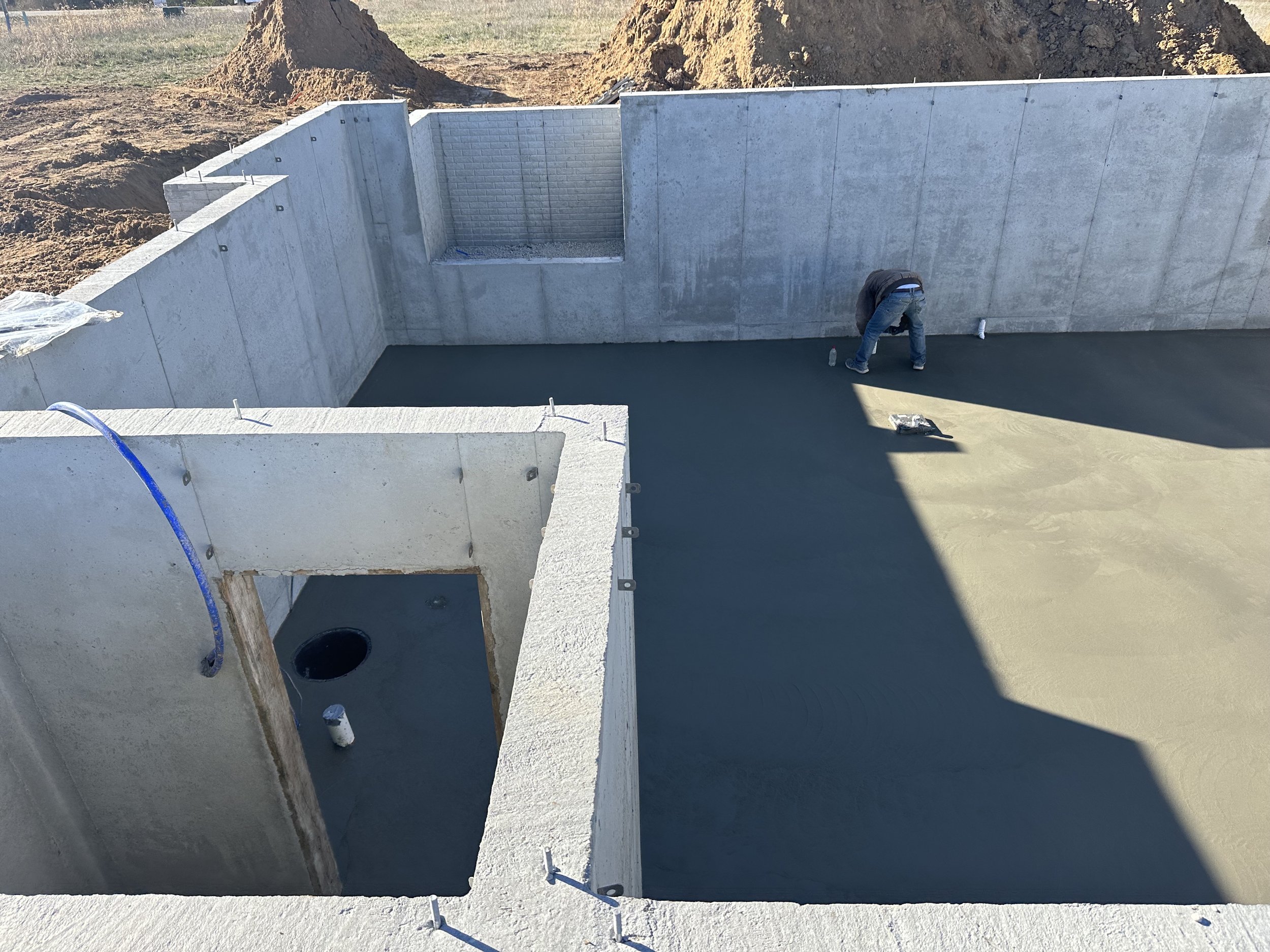
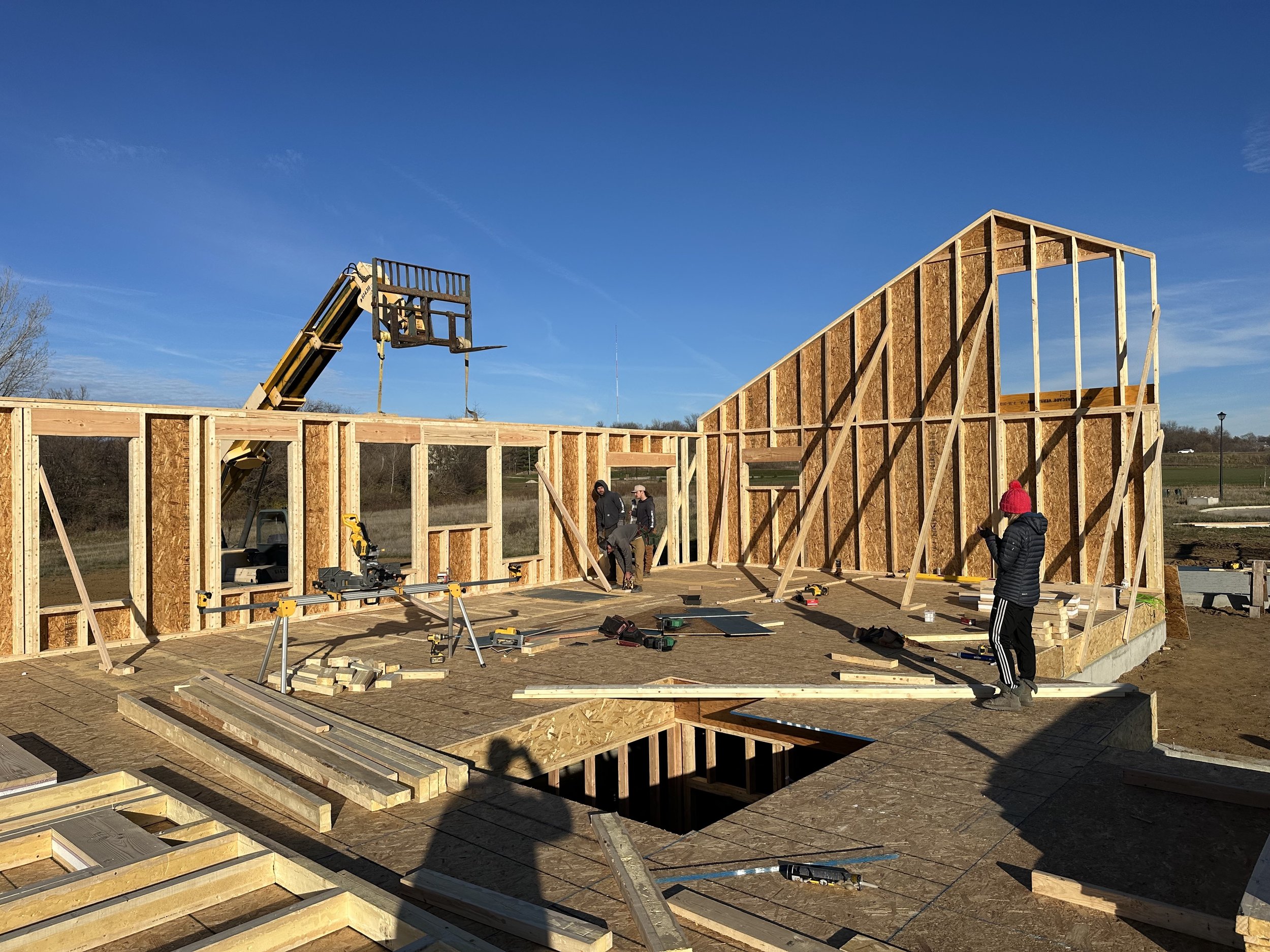
T-Studs
Timber Creek was built using T-Studs (Thermal Studs). These are essentially 2 separate studs linked together by 2.5” of closed-cell foam. These T-Studs get a thermal rating of R-19. This is an upgrade compared to a regular stud, which has a thermal rating of R-6.
They were selected to help solve the problem of thermal bridging. Thermal Bridging is heat loss through materials that don’t have great thermal resistance (R-value). These cold bridges make the home less comfortable and efficient. Wood tends to be a terrible insulator; however wood + foam solves that problem.
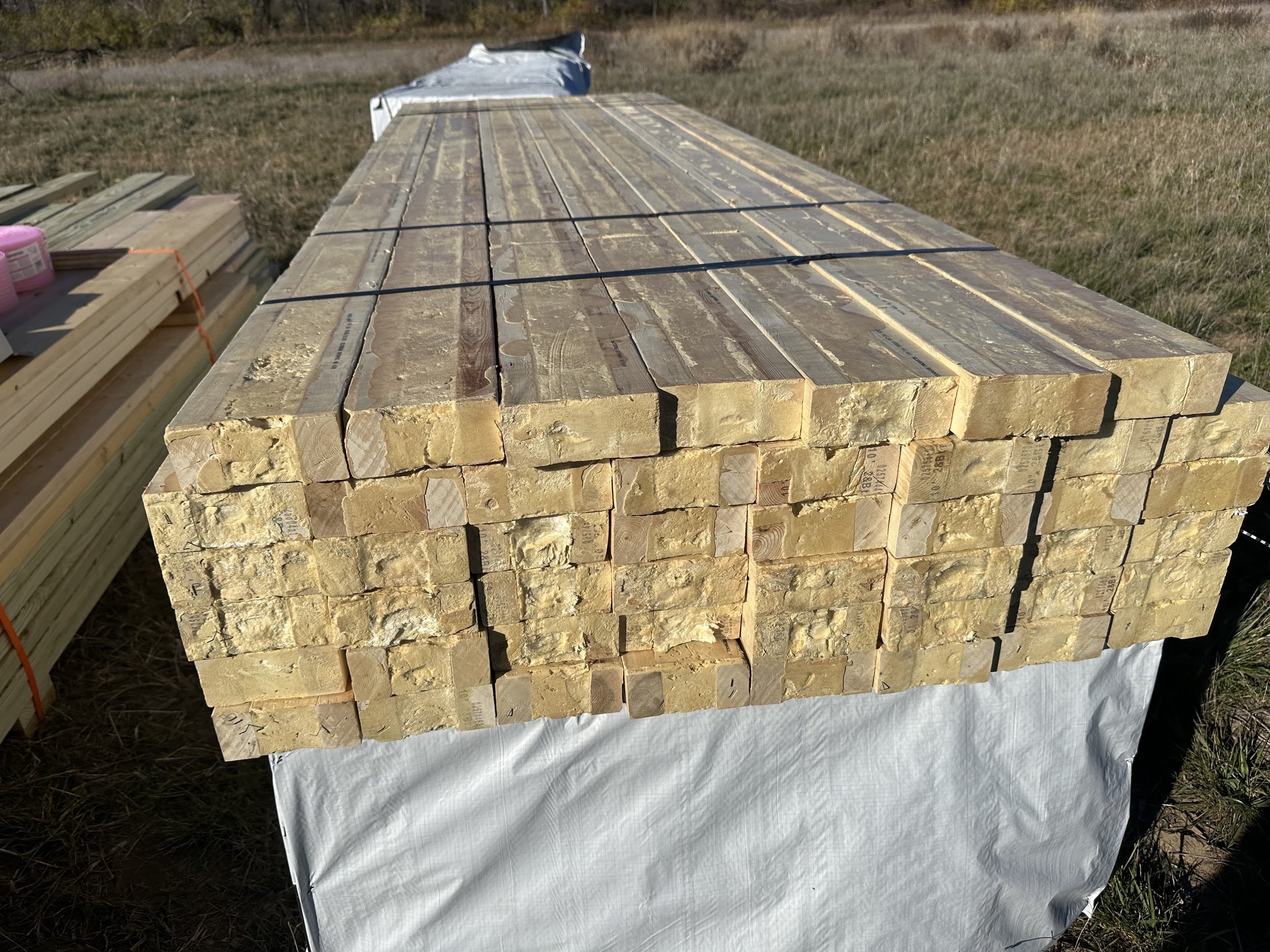

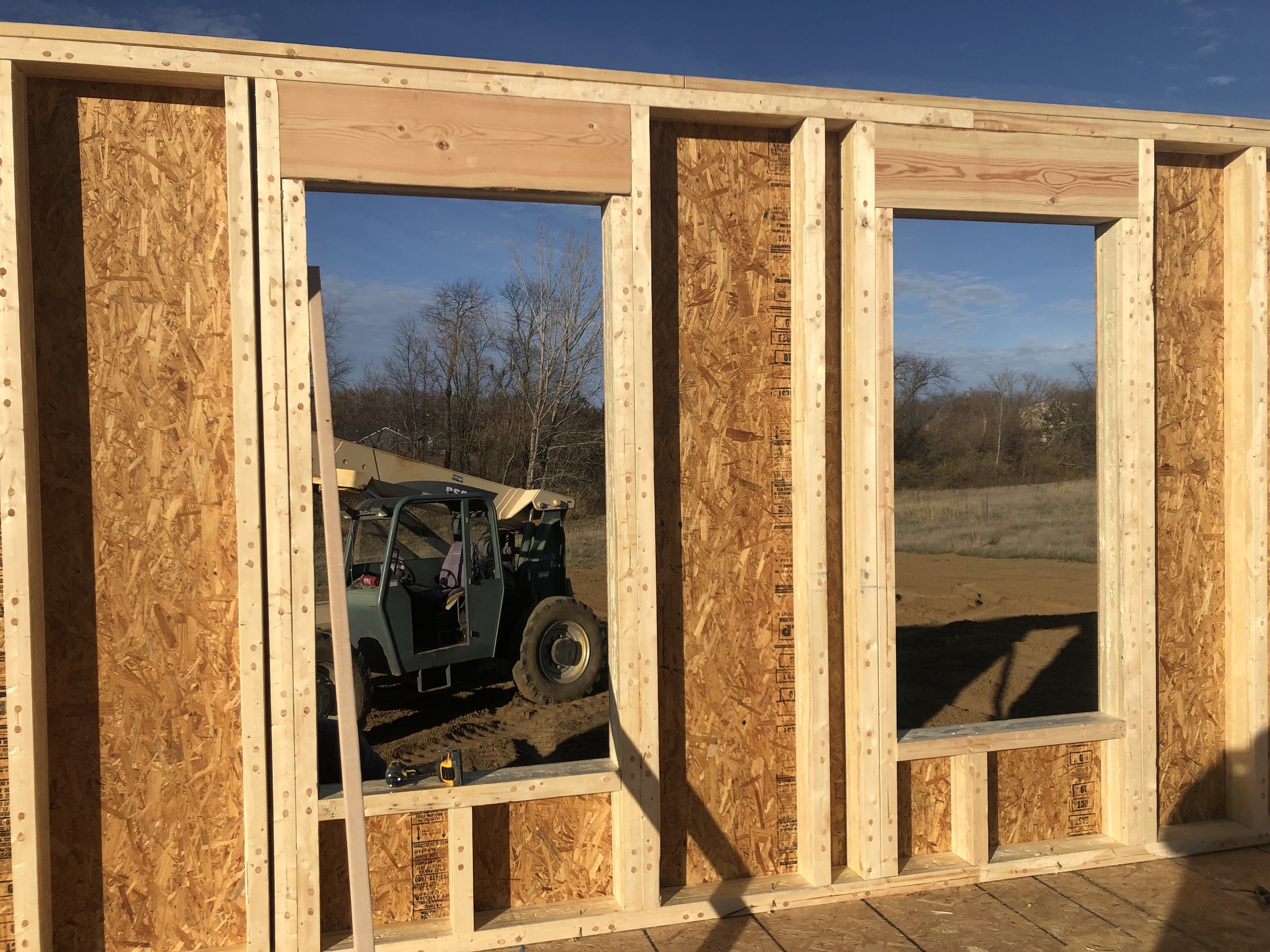
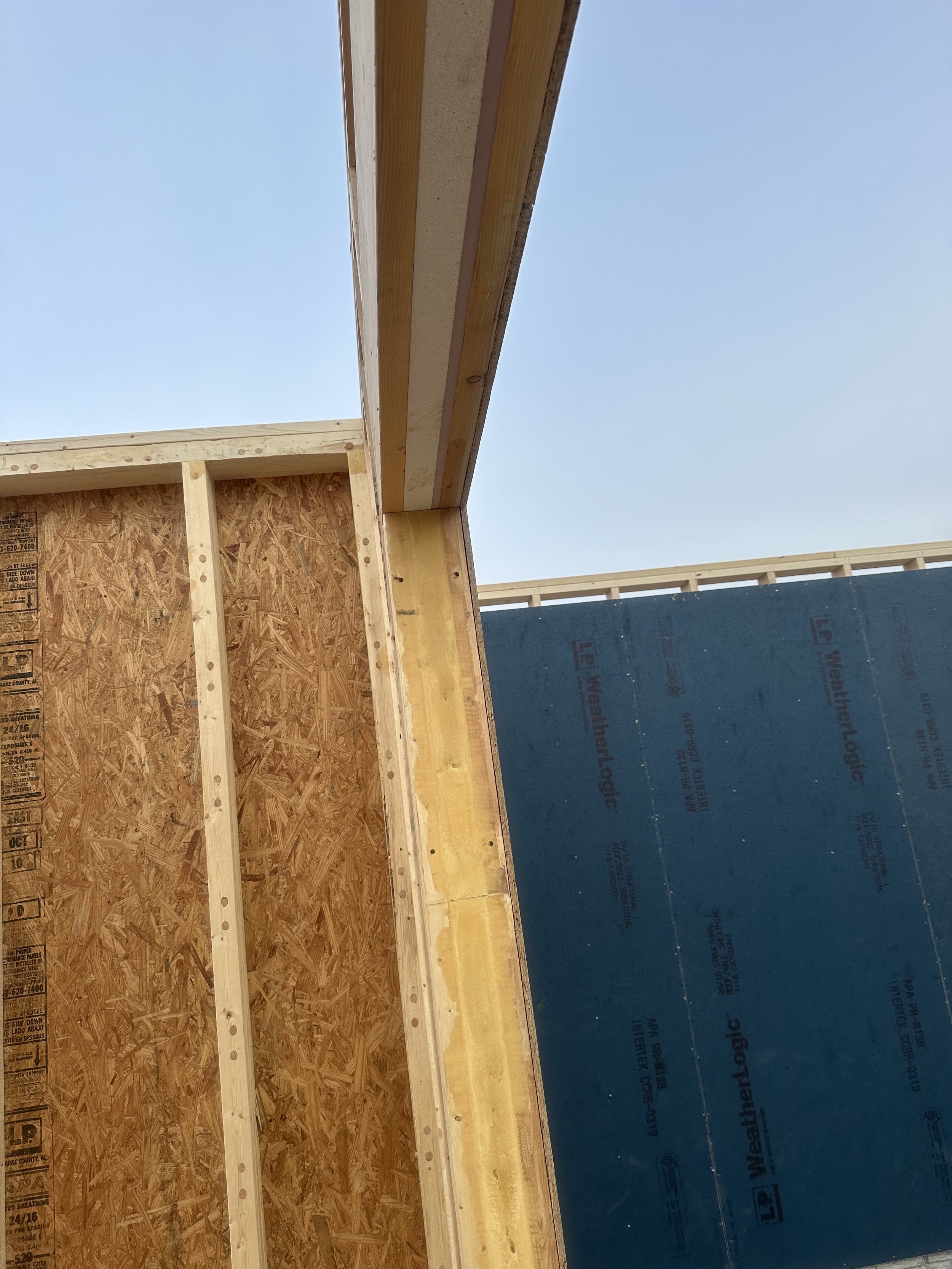
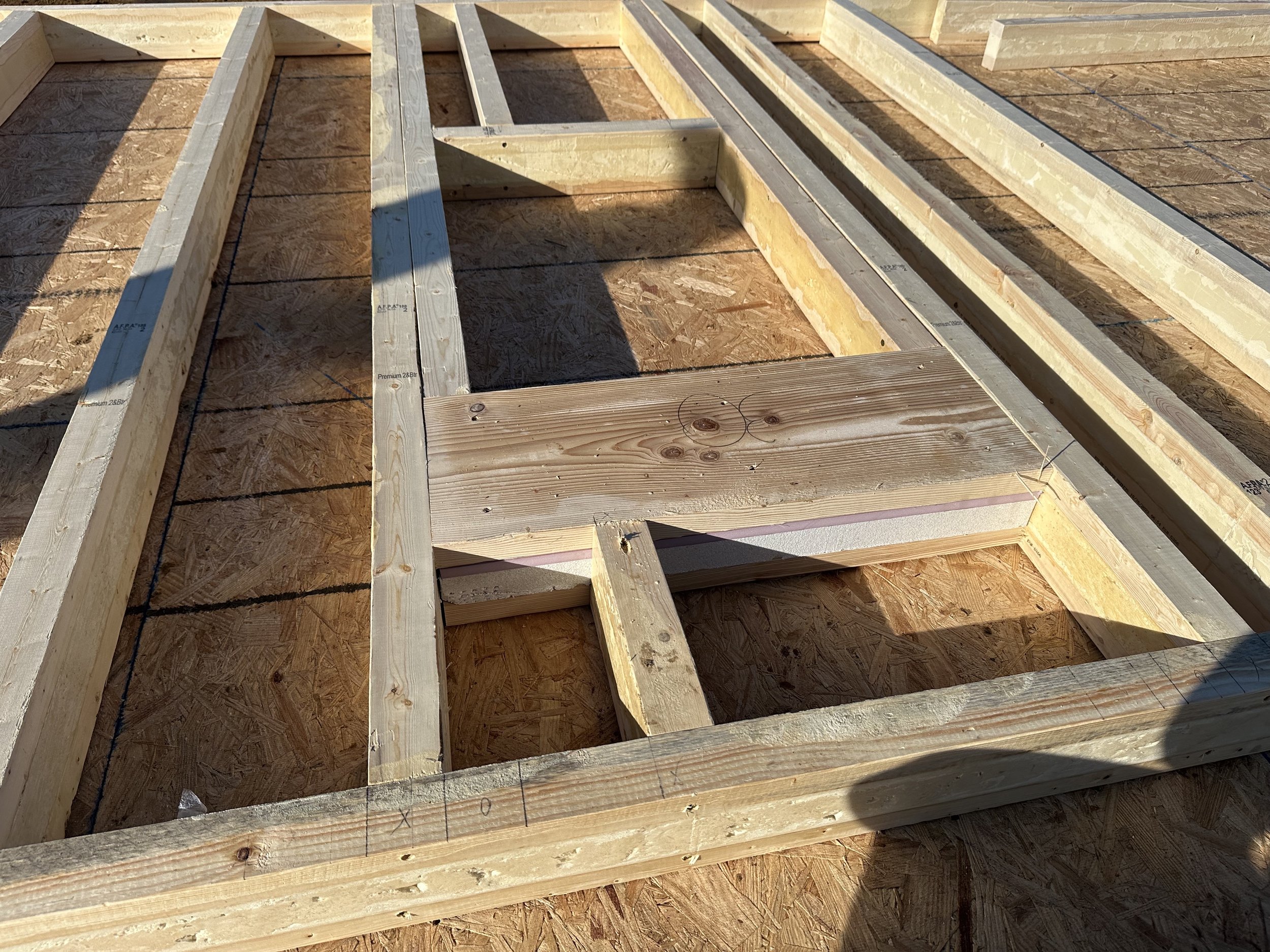
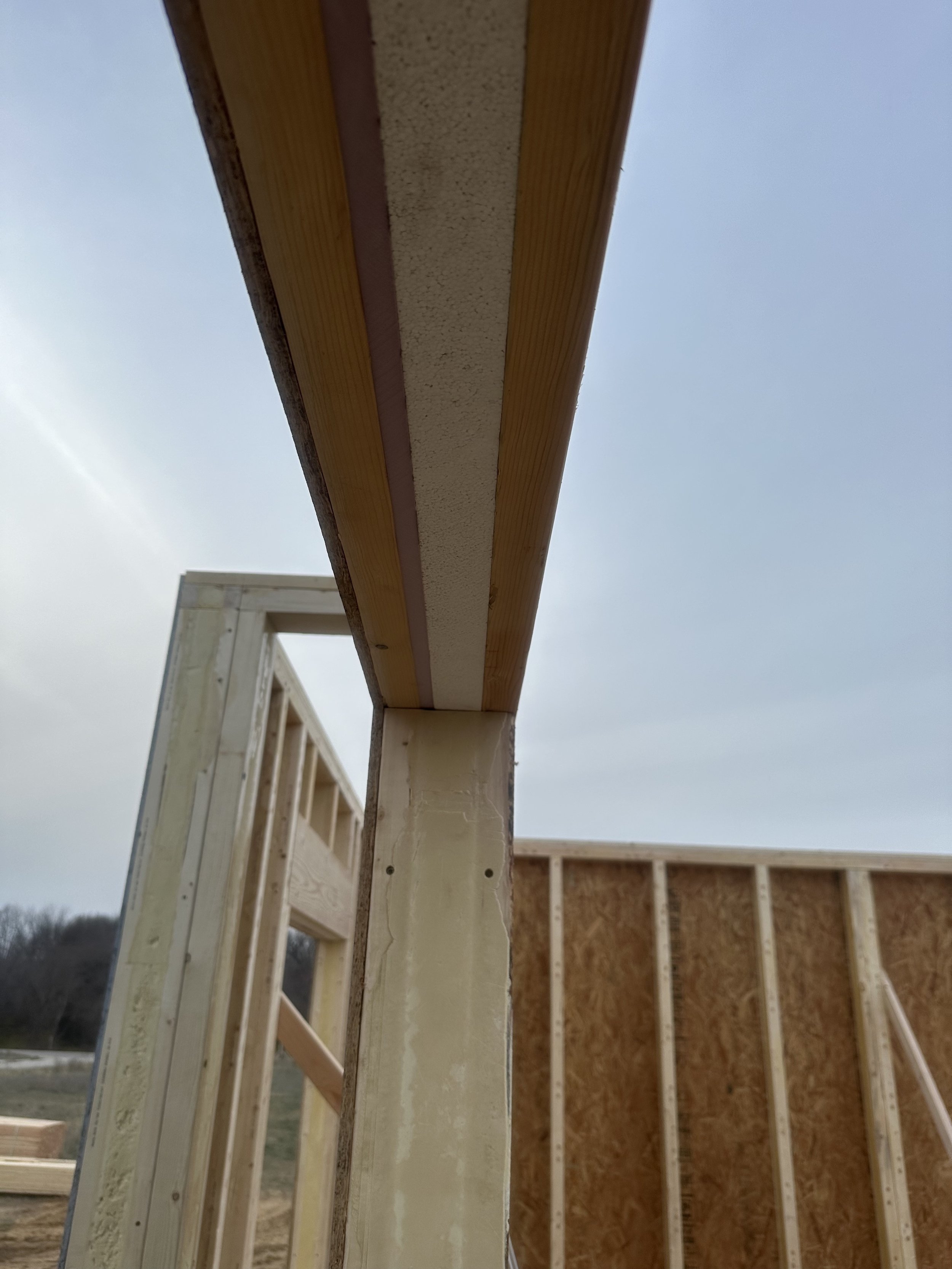
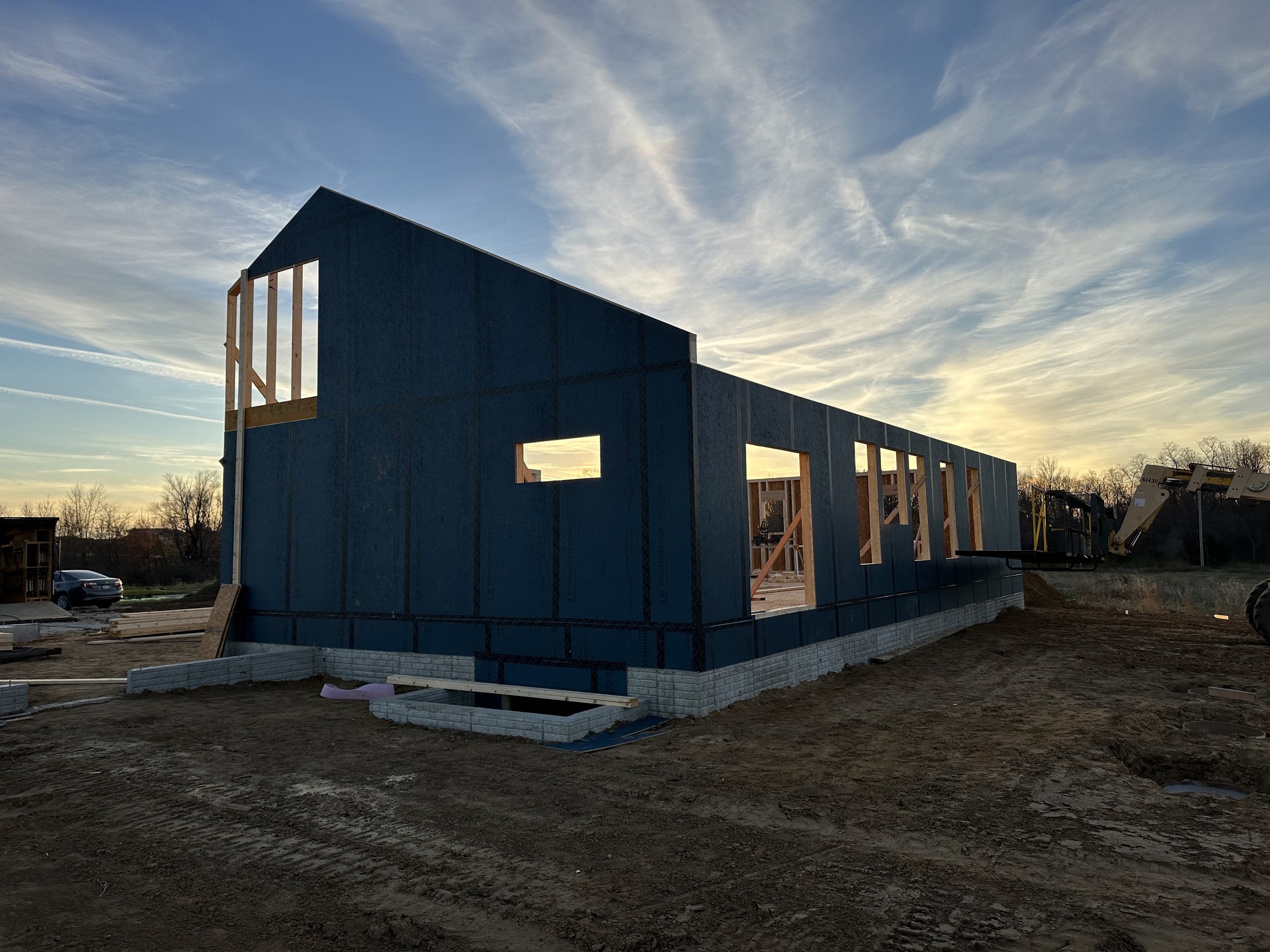
Exterior Shell & Sealants
Timber Creek’s exterior shell was built of WRB (weather resistant barrier) panels from Weather Logic. The exterior shell is one of the most overlooked opportunities for air-sealing. Because It is very difficult to properly seal WRB wraps (for example, Tyvek) homeowner Jacob Heffernen opted for WRB panels.
The connection between the blue-board and the foundation wall itself was diligently sealed with weather-resistant caulking. In the video below, you can see Jacob’s meticulous dedication to air-sealing his home as he covers every blue-board seam and nail hole with sealant tape.
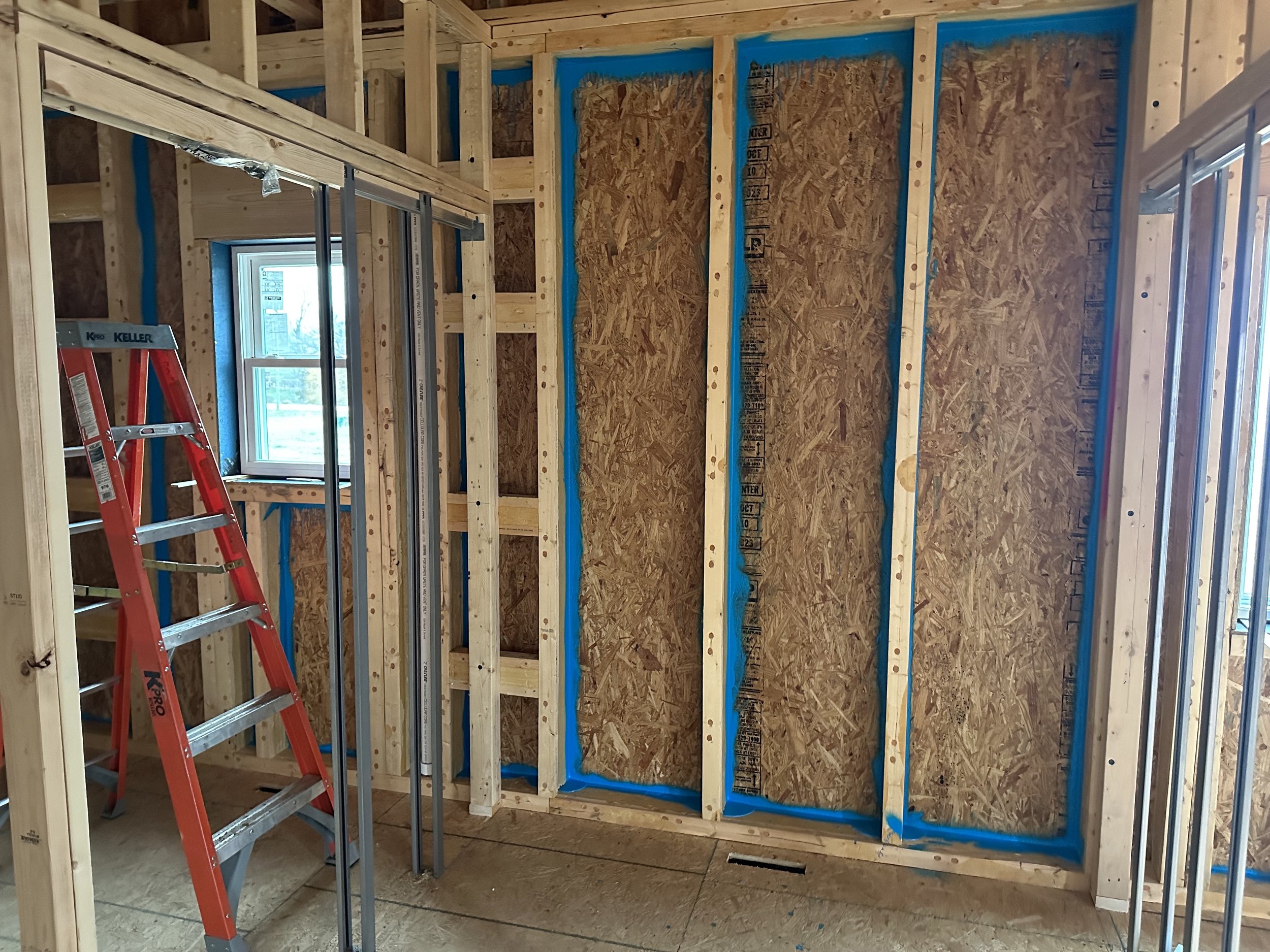
Interior Sealant: EcoSeal
After the rough-in stage of Timber Creek was complete, Thermal Shop set its sight on air-sealing. An easy way to understand the importance of air-sealing is this: imagine you are wearing a wool sweater on a cool, windy day. Are you warm? Or, does the wind sneak easily through the fibers of your wool sweater? Air-sealing on a house is like putting on a wind-breaker over your wool sweater. Now you are warm, and protected from the never ceasing movements of the air.
Thermal Shop applied EcoSeal by spraying it picture-frame style on every 1st floor bay. After an initial bout of good luck with the product it became difficult to apply to the top and bottom plates. In the end, Thermal Shop used a putty knife to cover every seam in the framing.
For finishing touches, Thermal Shop used can foam to seal outlets, cable penetrations, and around windows and doors.

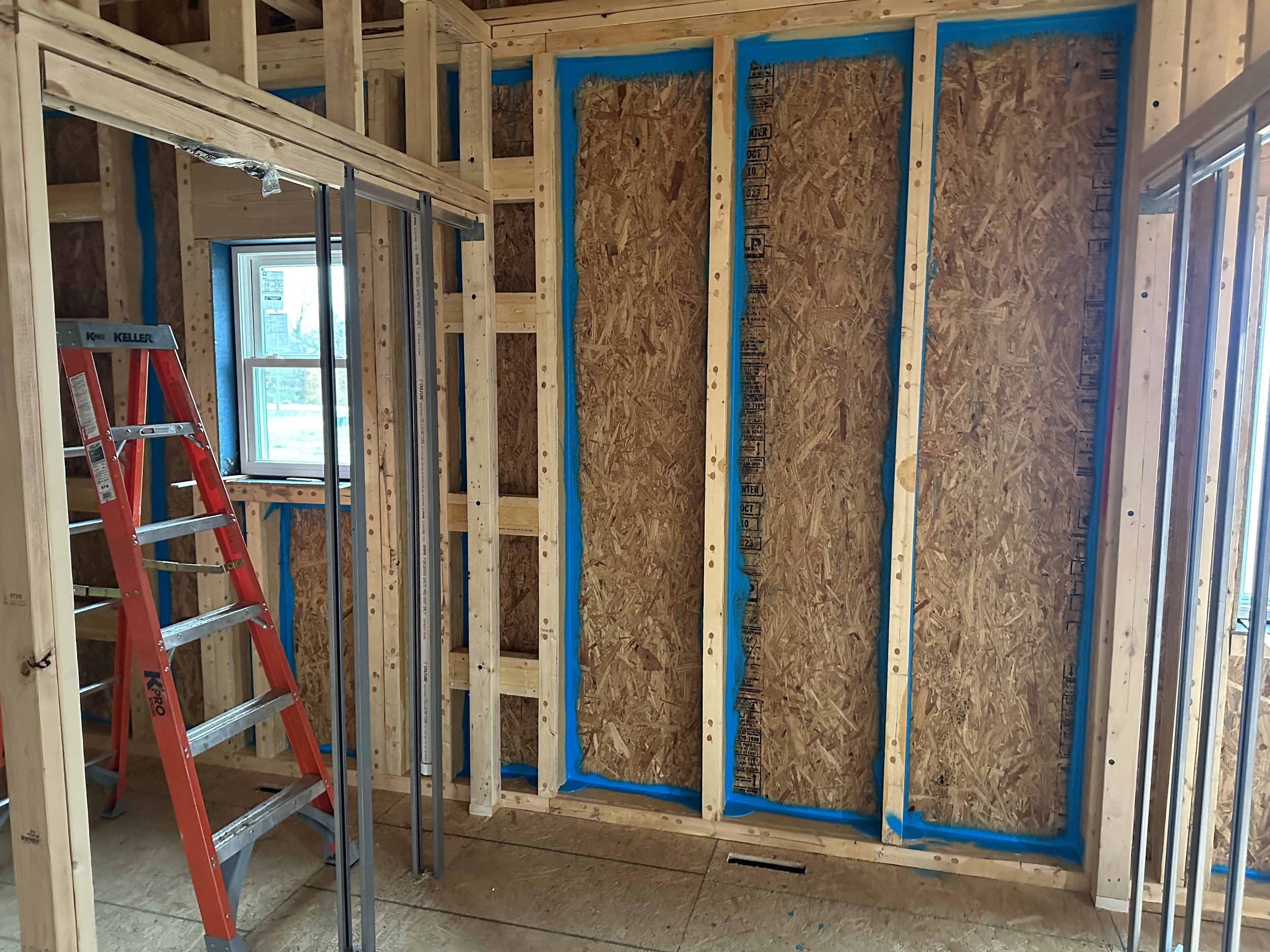
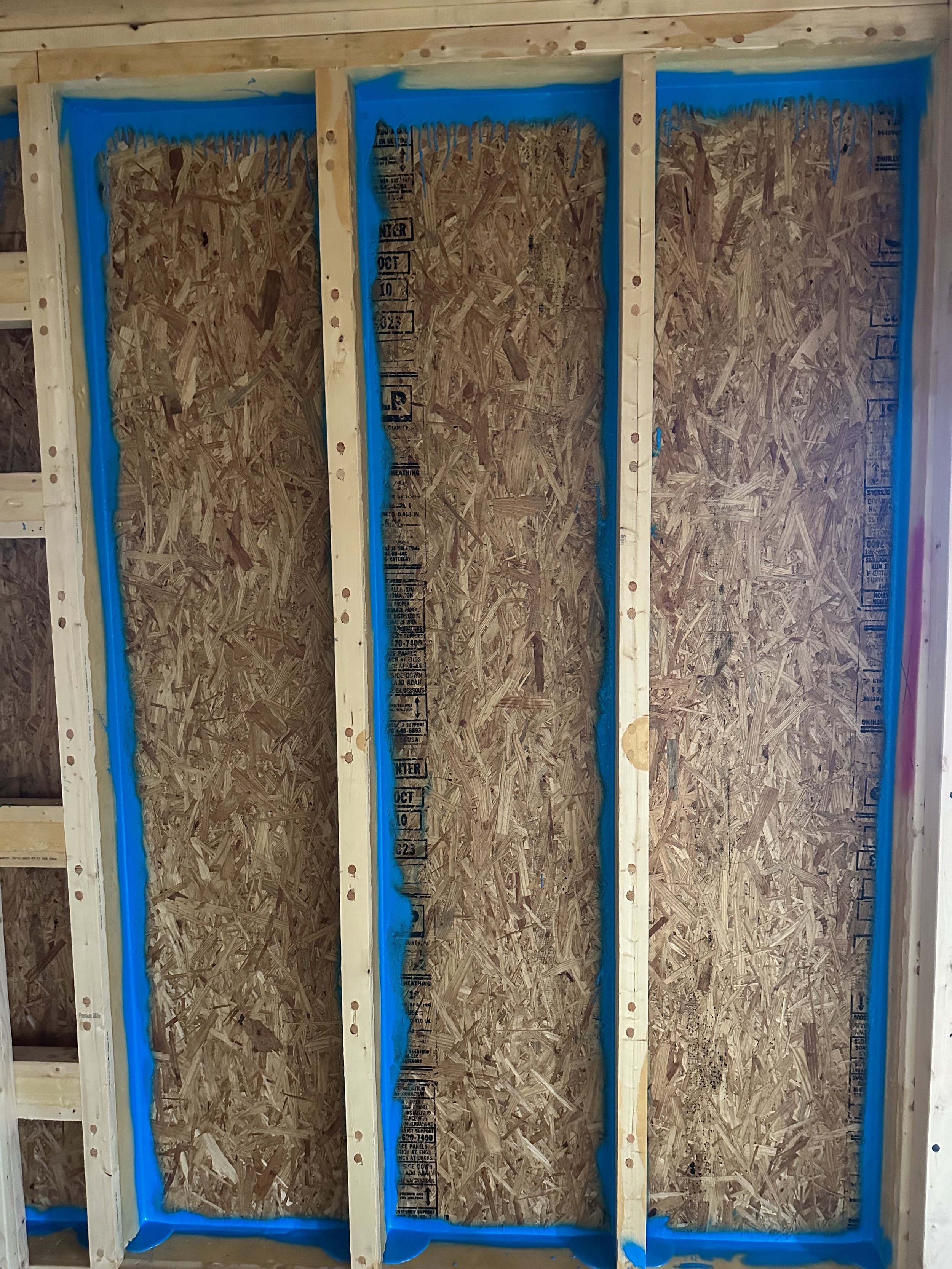
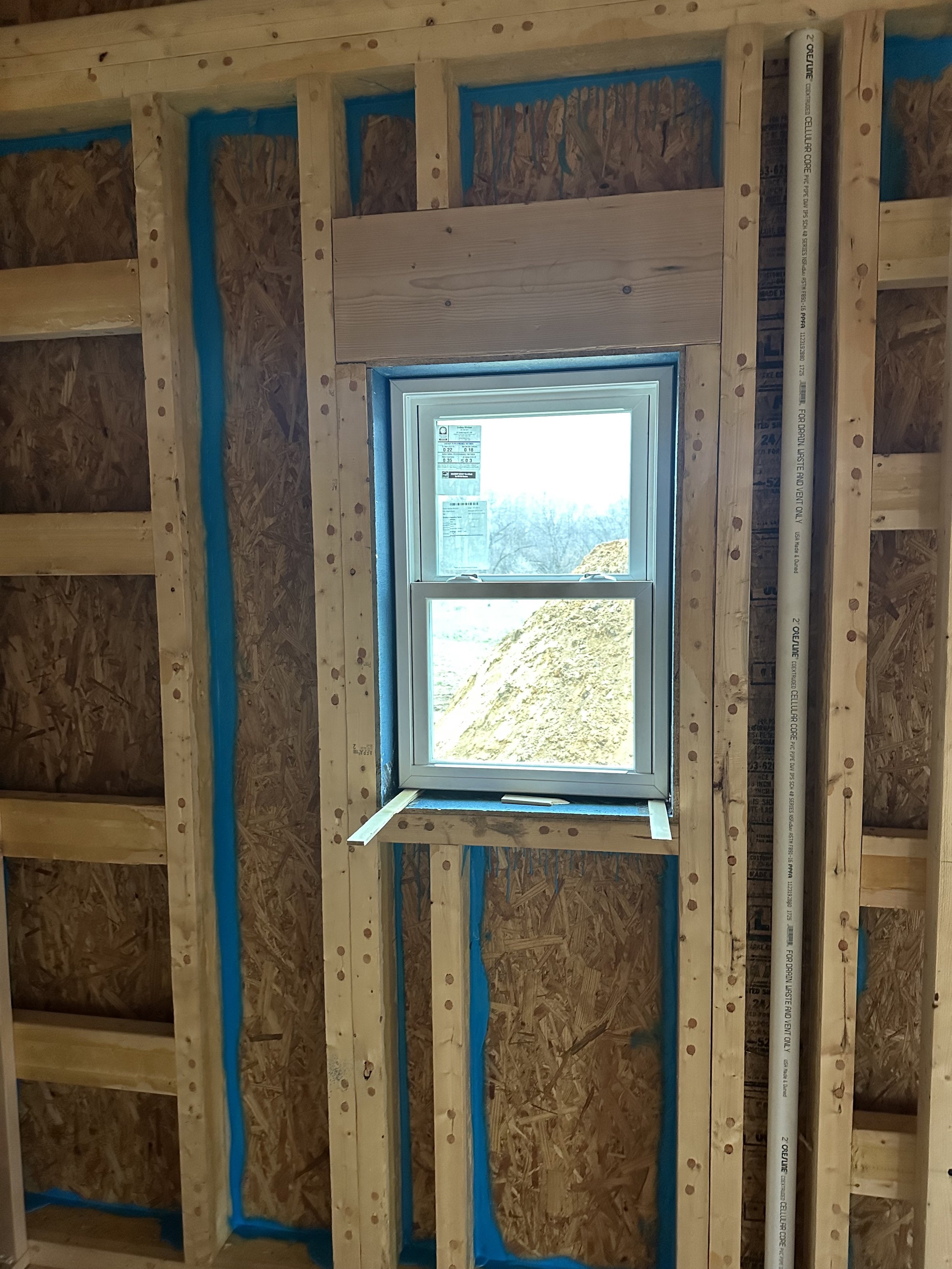
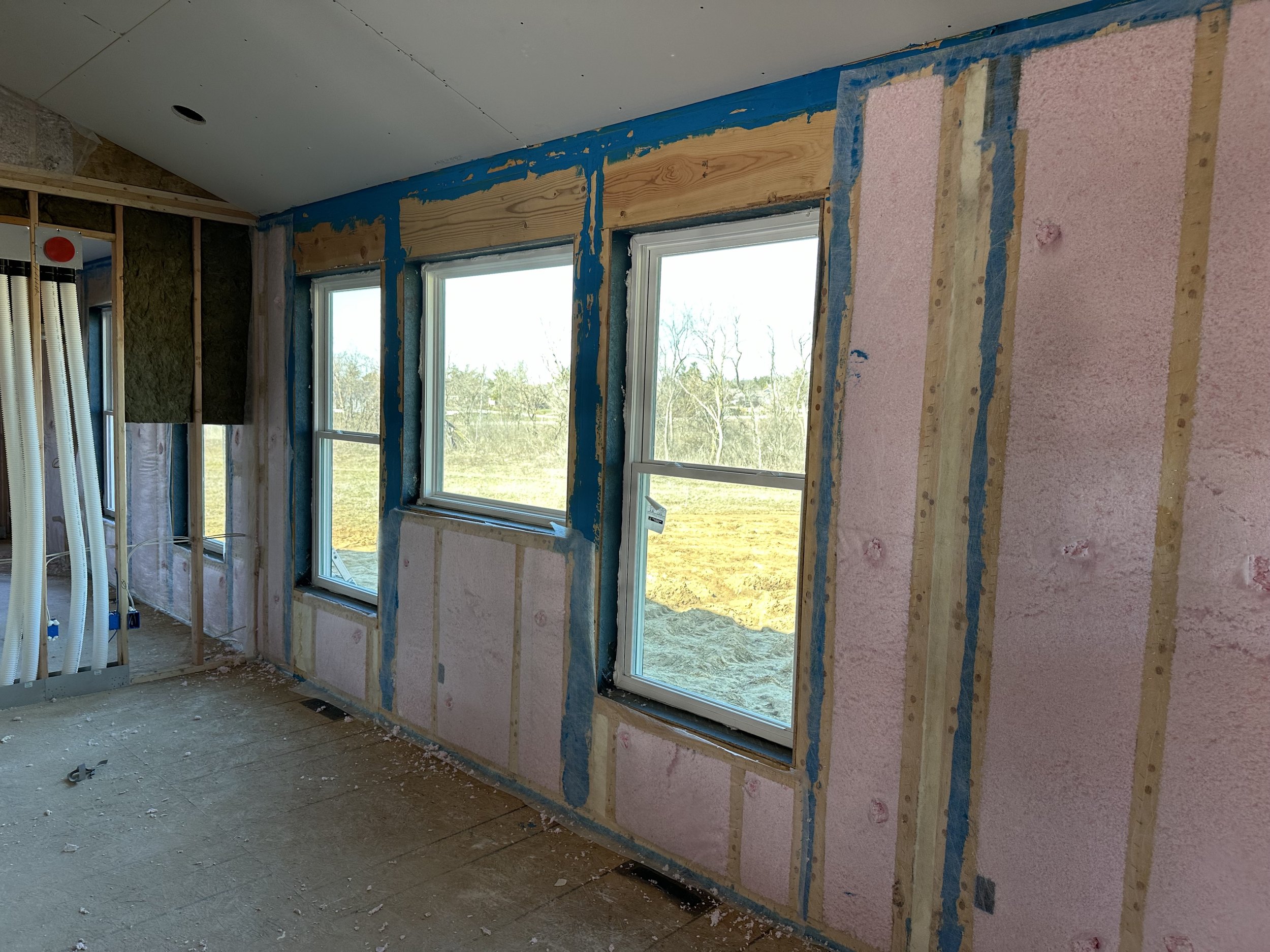
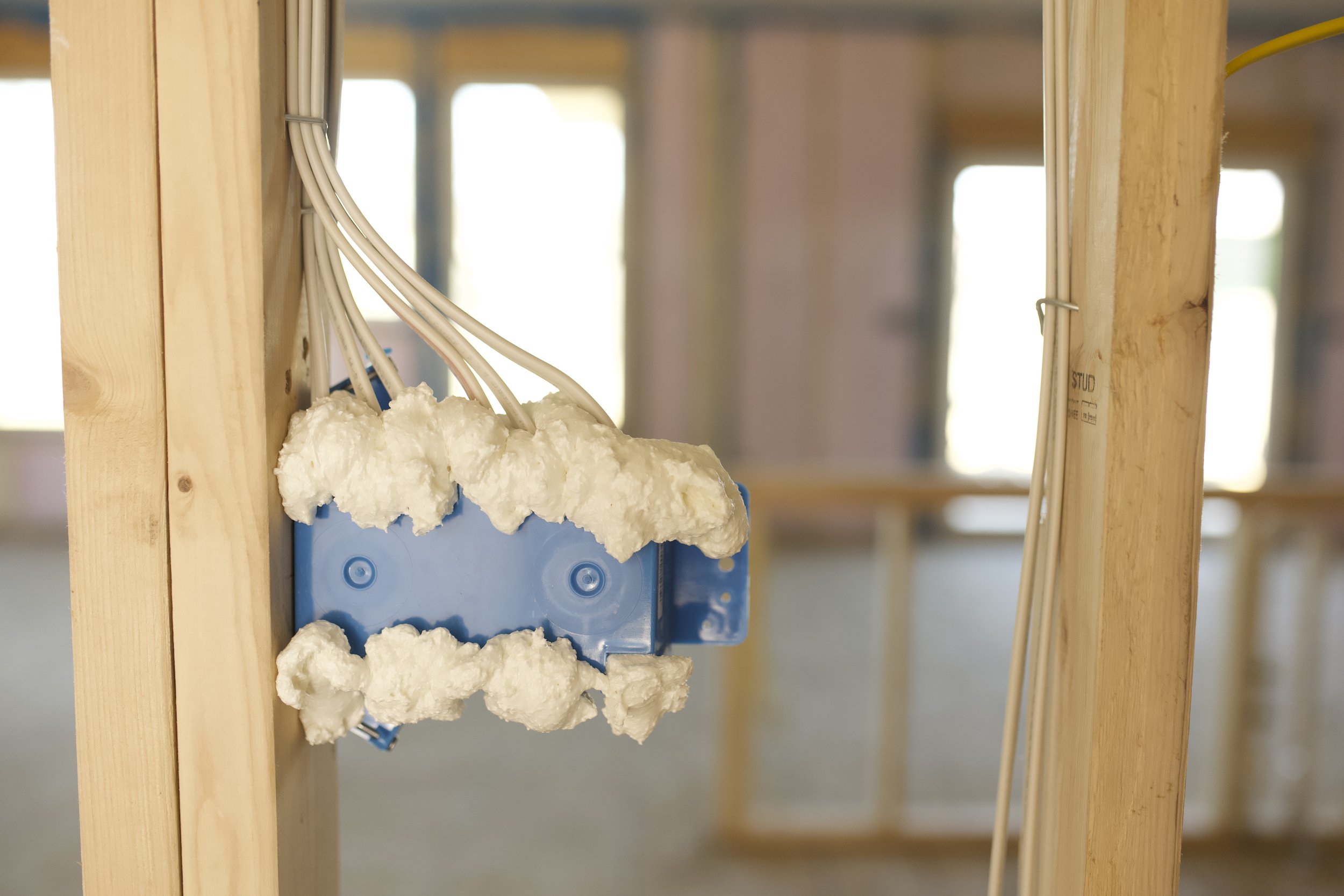
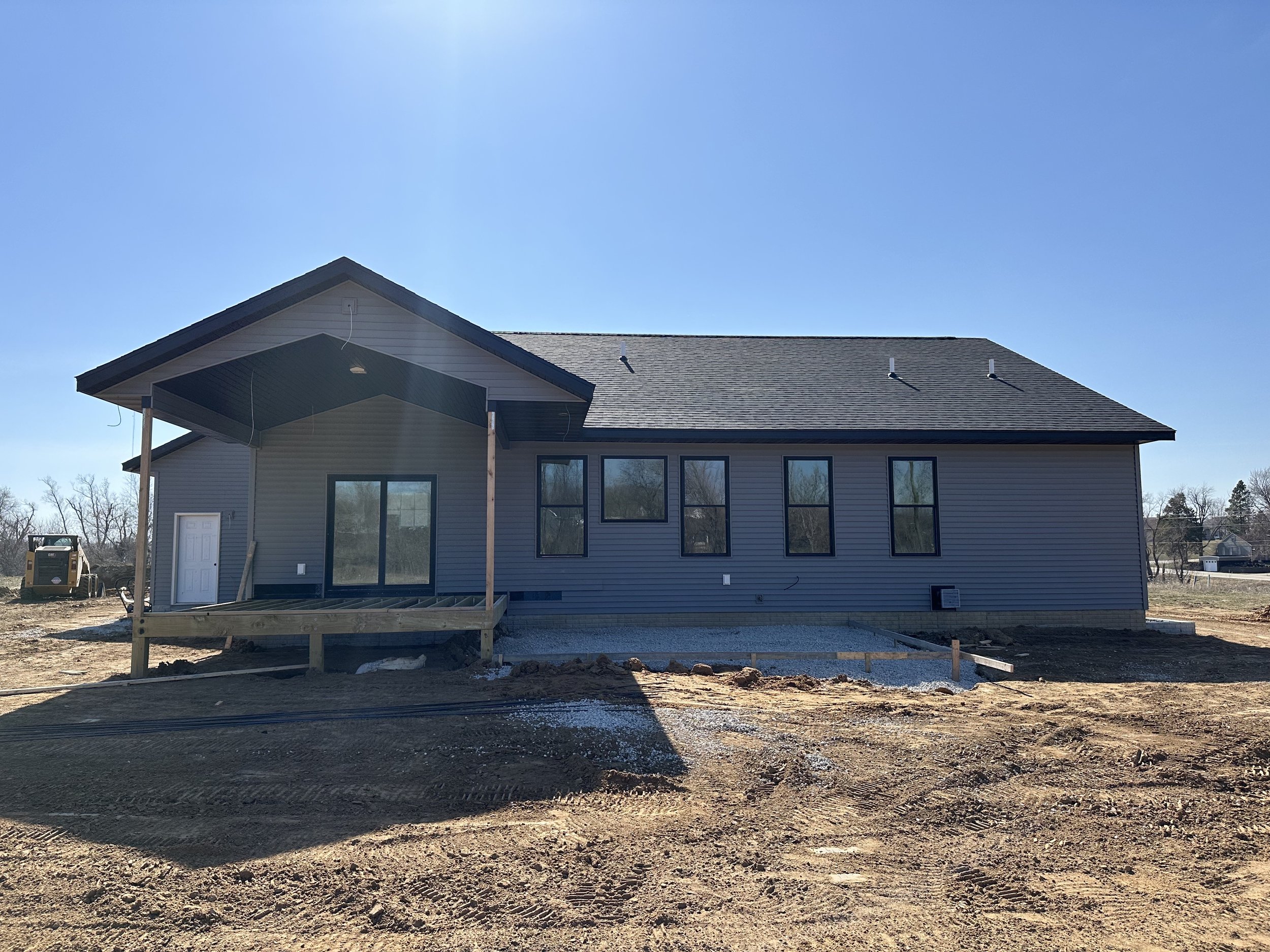
Windows
The average window in Iowa’s climate zones has a thermal rating between R-3 and R-4. Because of this, one of the biggest sources of heat loss in houses and buildings is their windows. To mitigate potential heat loss, Timber Creek was fitted with argon-filled triple-pane windows.
These are exactly what they sound like: 3 panes of glass sandwiching two argon gas-filled spaces. Argon is less heat conductive than air, making it an excellent thermal barrier. Overall, Timber Creek’s windows get about 50% more R-value than the average window.
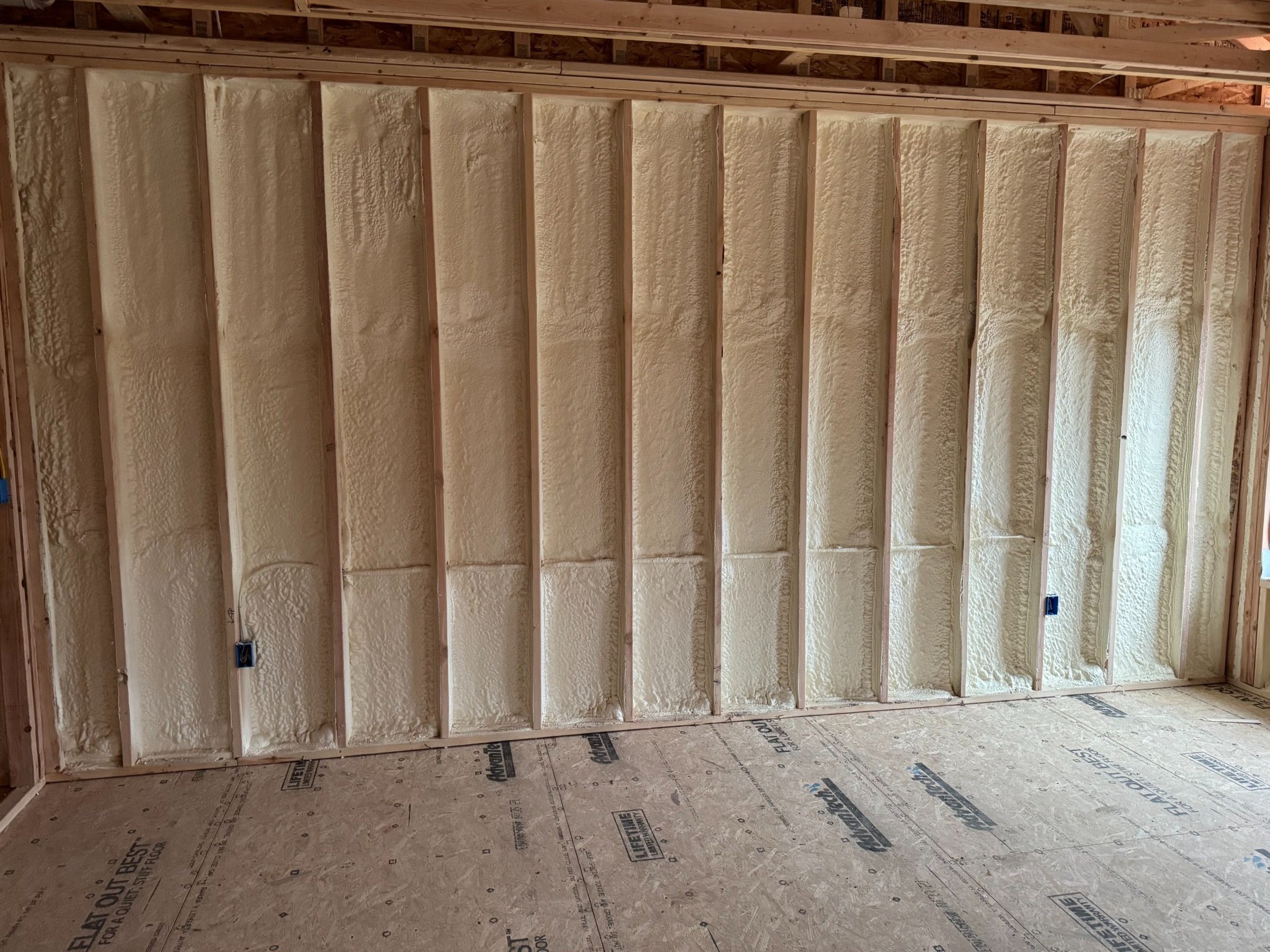
Closed Cell Spray Foam
Spray Foam was used to insulate all difficult-to-reach areas. For example, behind plumbing lines, inside thin cavities, inside corners, and throughout the rim joist. Spray foam was also installed around all attic penetrations, top plates, and air chutes.
Thermal Shop also installed 2” of closed cell spray foam on foundation walls to keep moisture out. This ensures a dryer and more comfortable basement.
Under the front porch-typically a storage space- is notoriously wet. To mitigate potential moisture collection, 2” of EPS foam board were installed before pouring concrete. Then the underside was spray-foamed with 2” of closed cell.
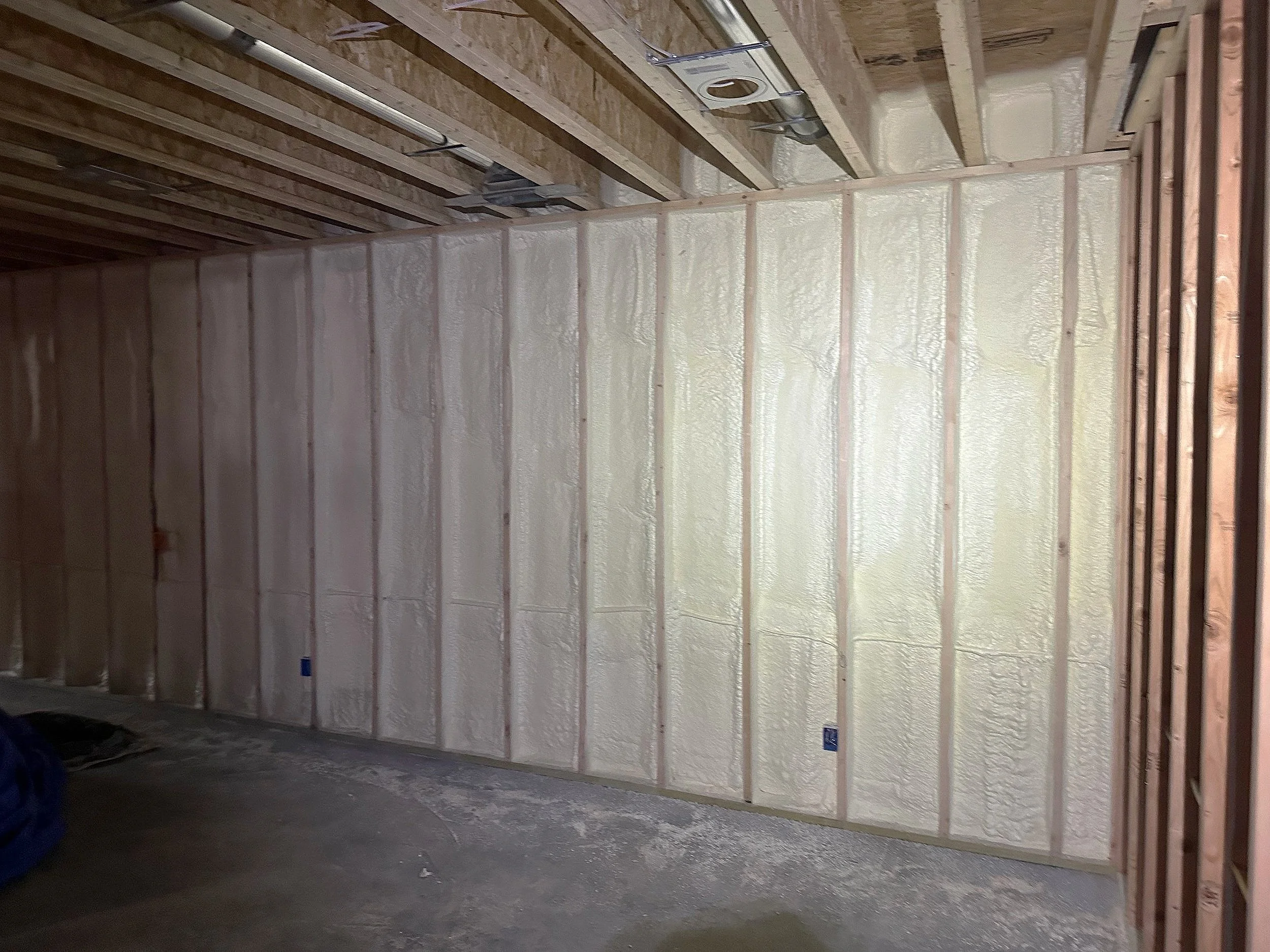
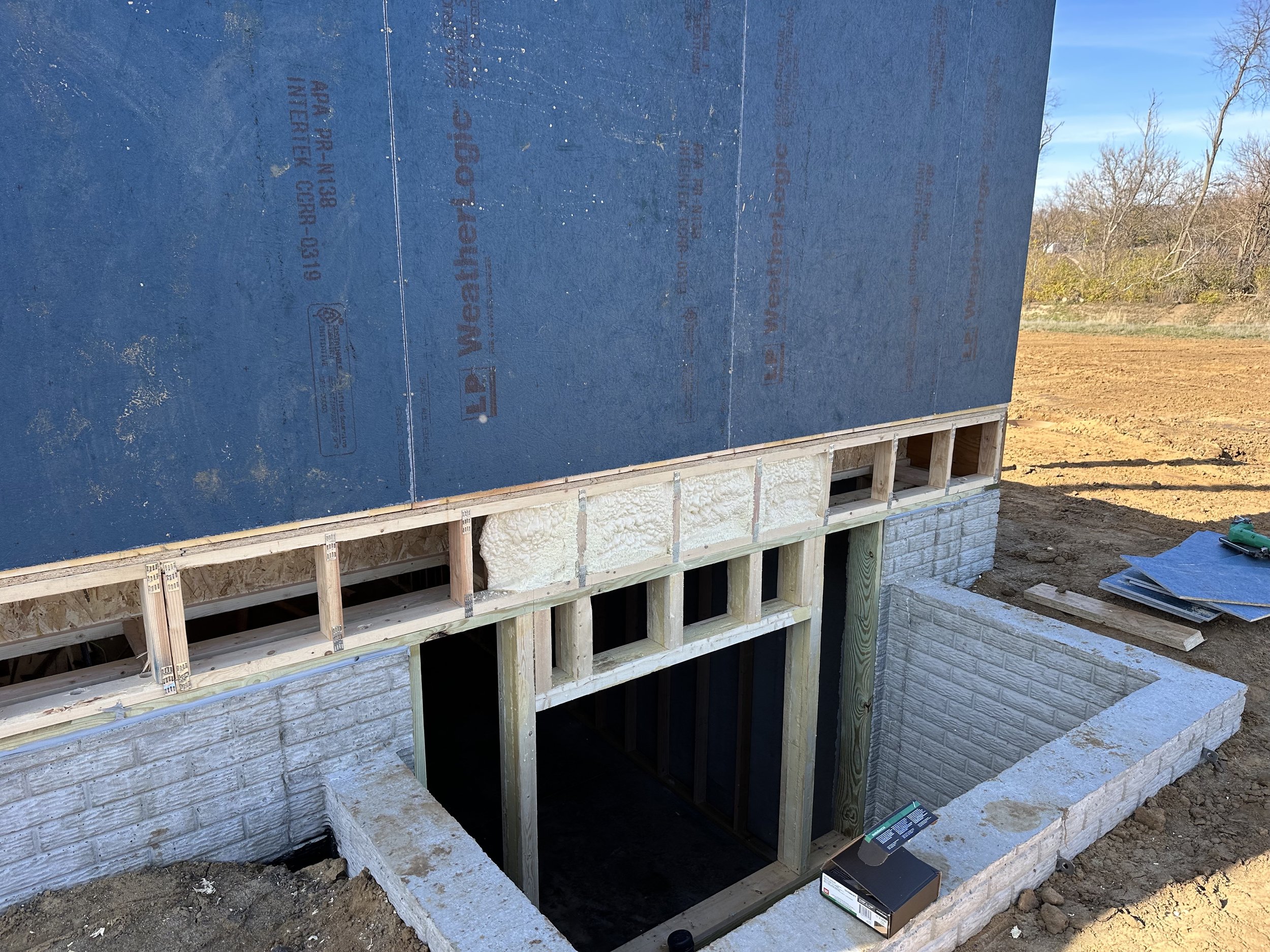
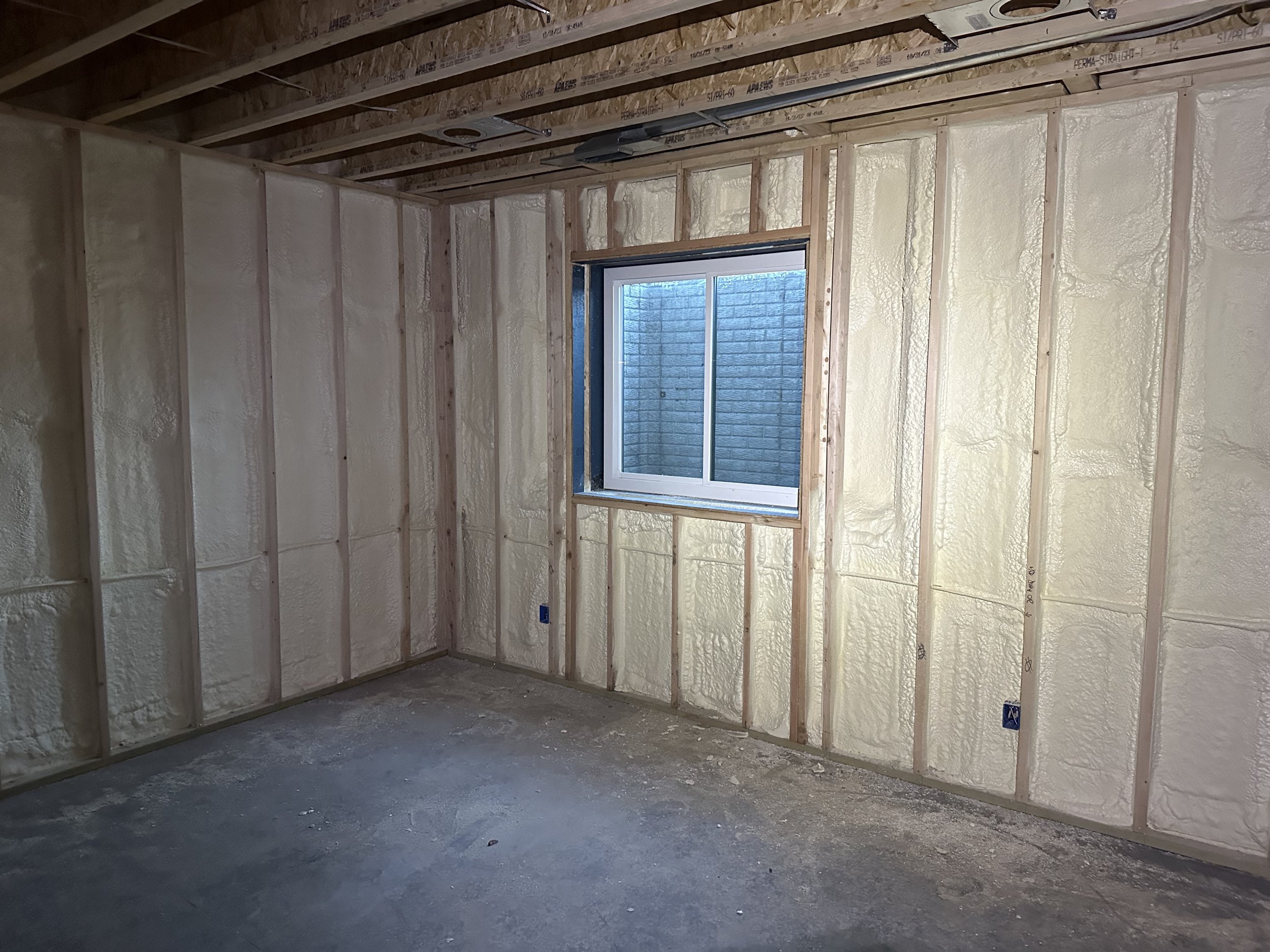
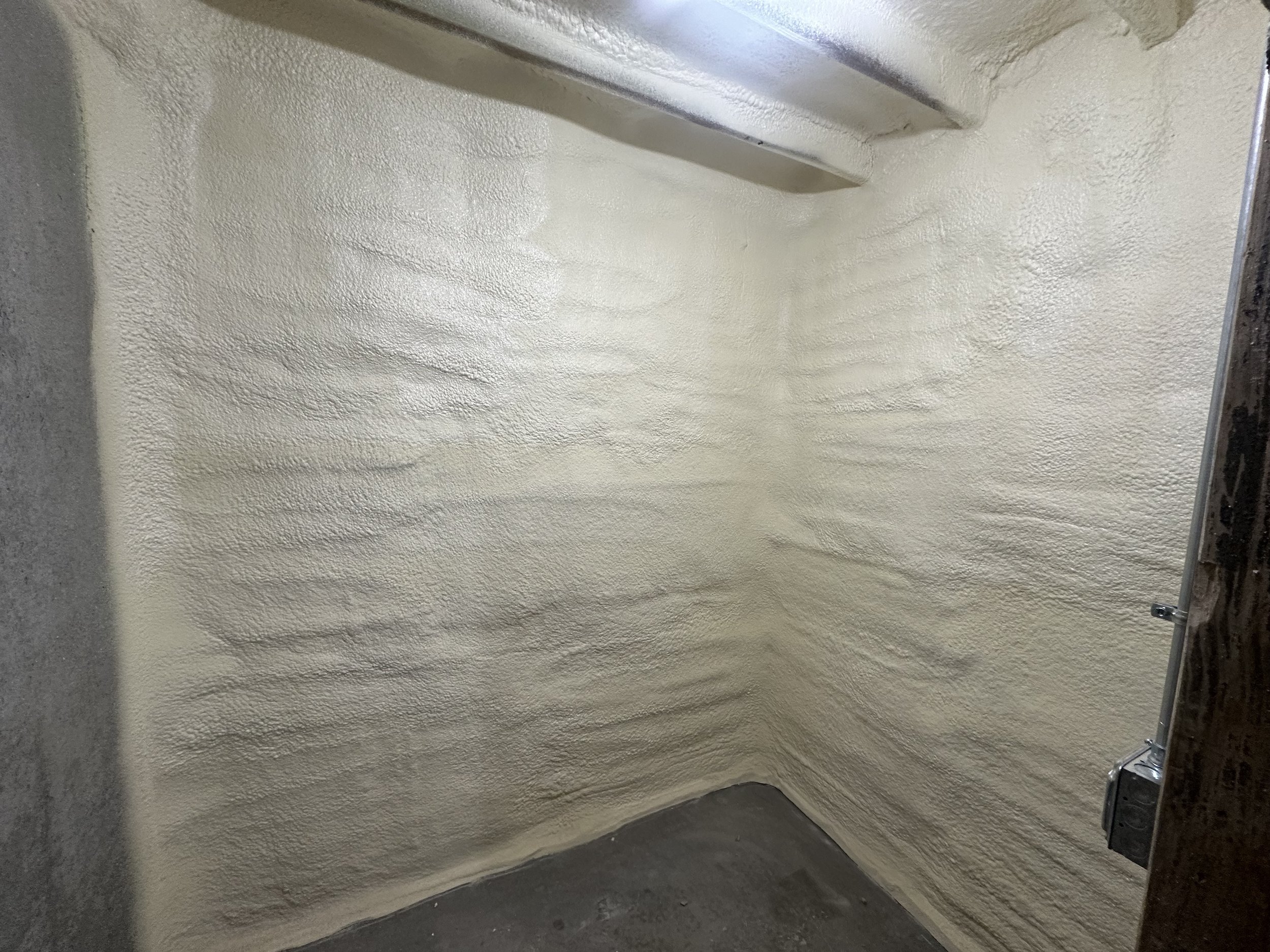
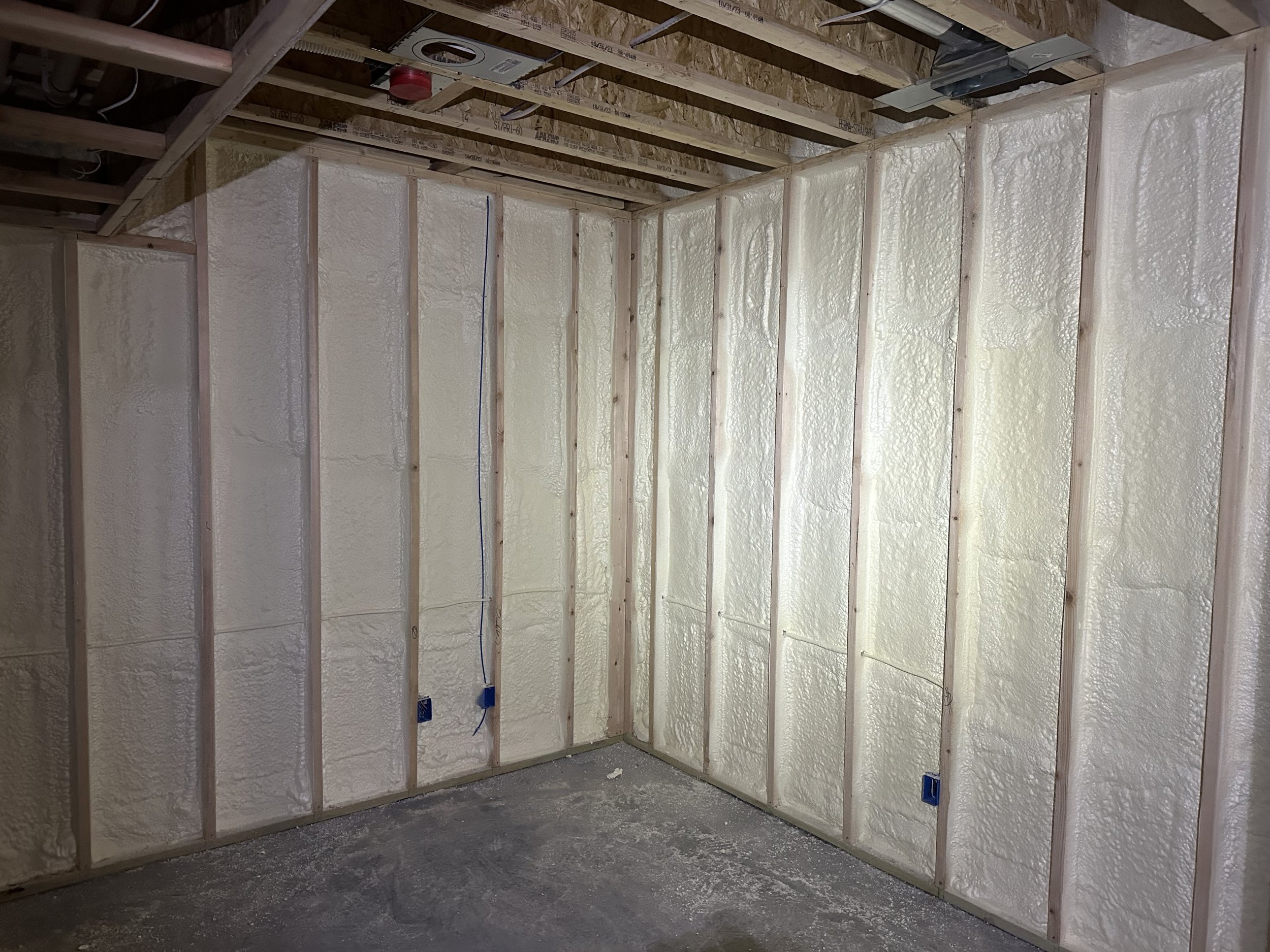
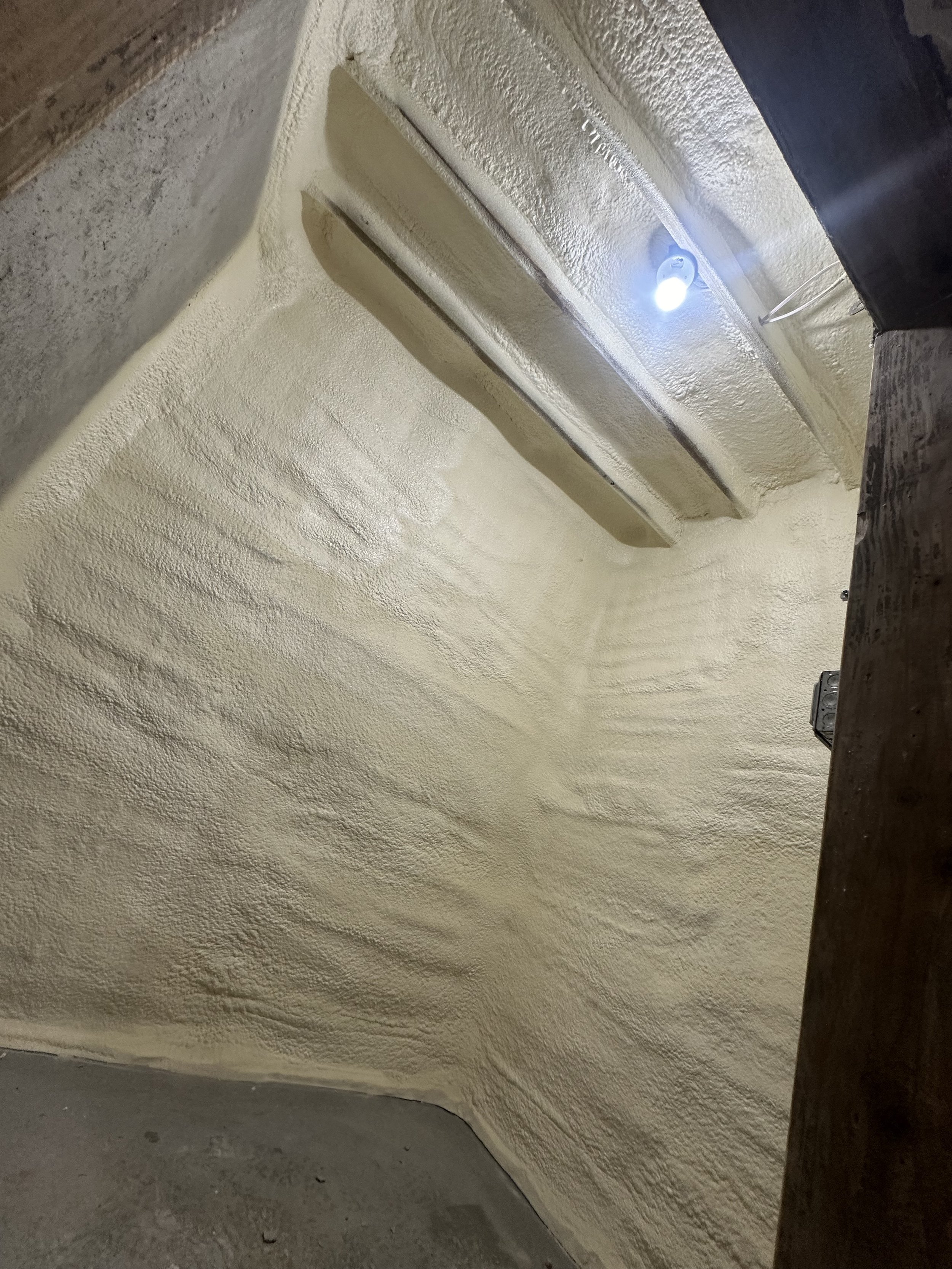
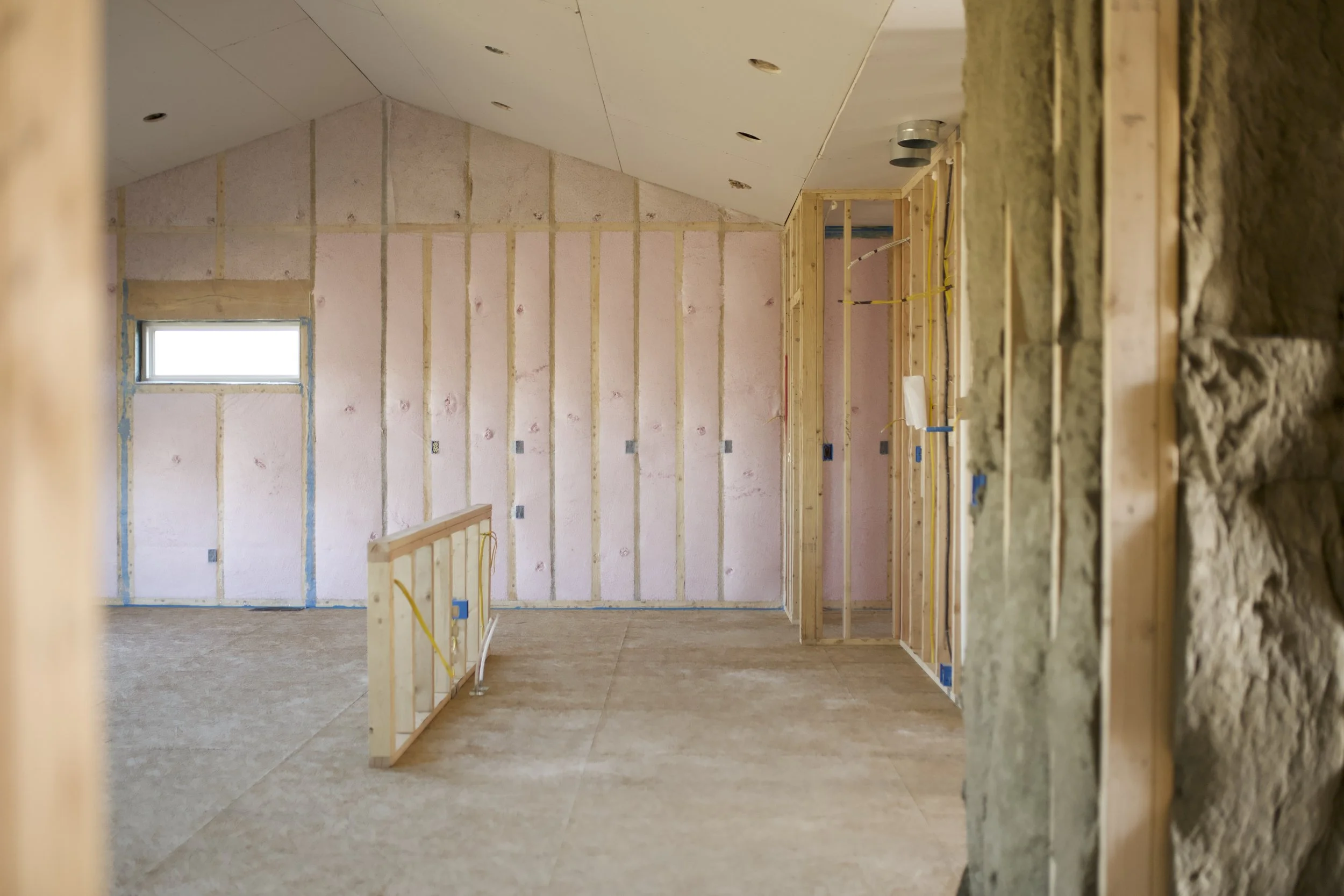
Fiberglass Net & Blow
To start the net & blow application process, breathable mesh netting went up stapled to main floor exterior wall studs with a pneumatic stapler. Next, fiberglass insulation was blown in. A dense-pack application provided a thermal barrier rating of R-23+ on all 2x6 walls. This installation was selected for its dense-pack ability and for easy application behind wires, boxes, pipes, and other obtrusions.
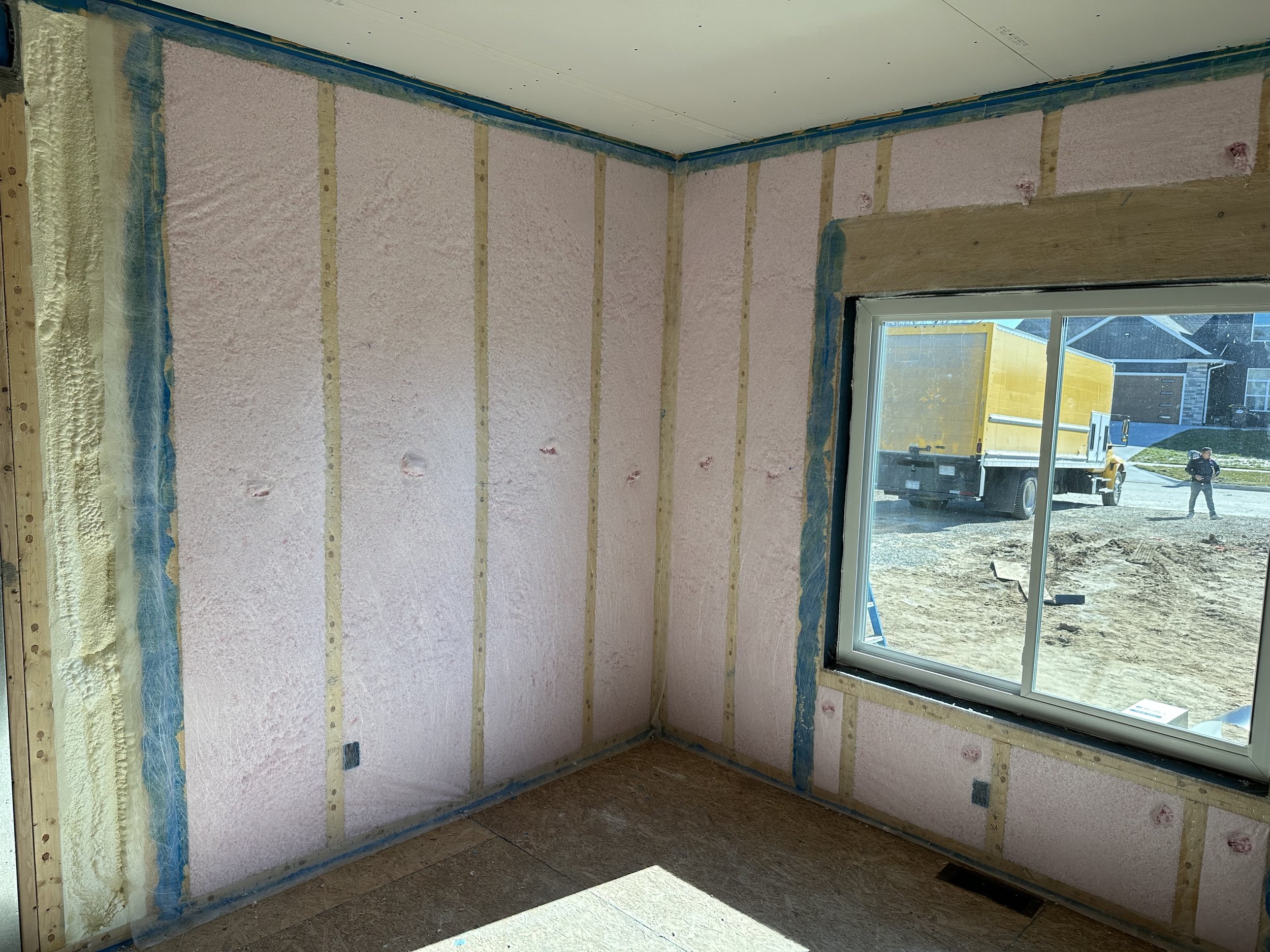

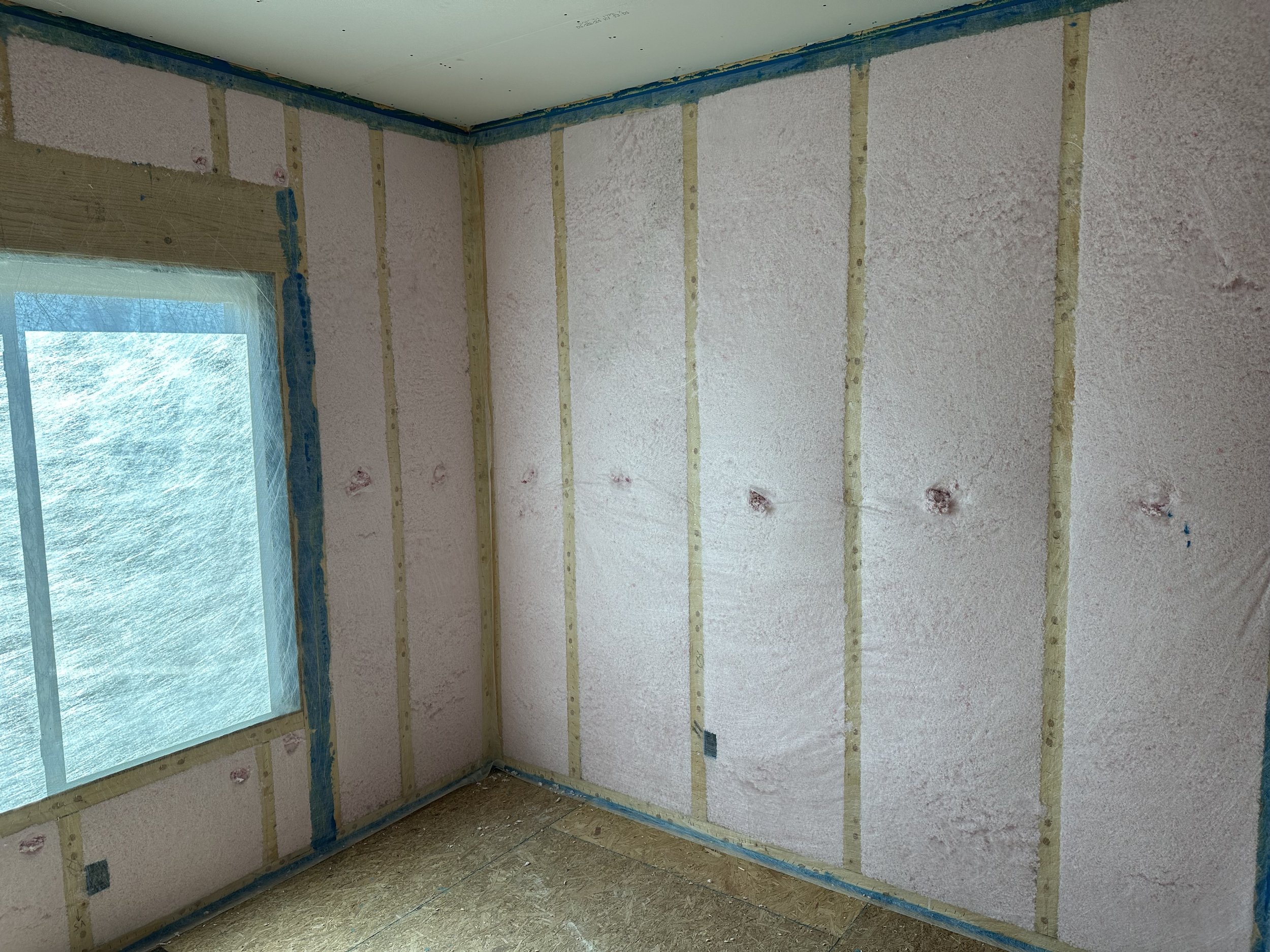
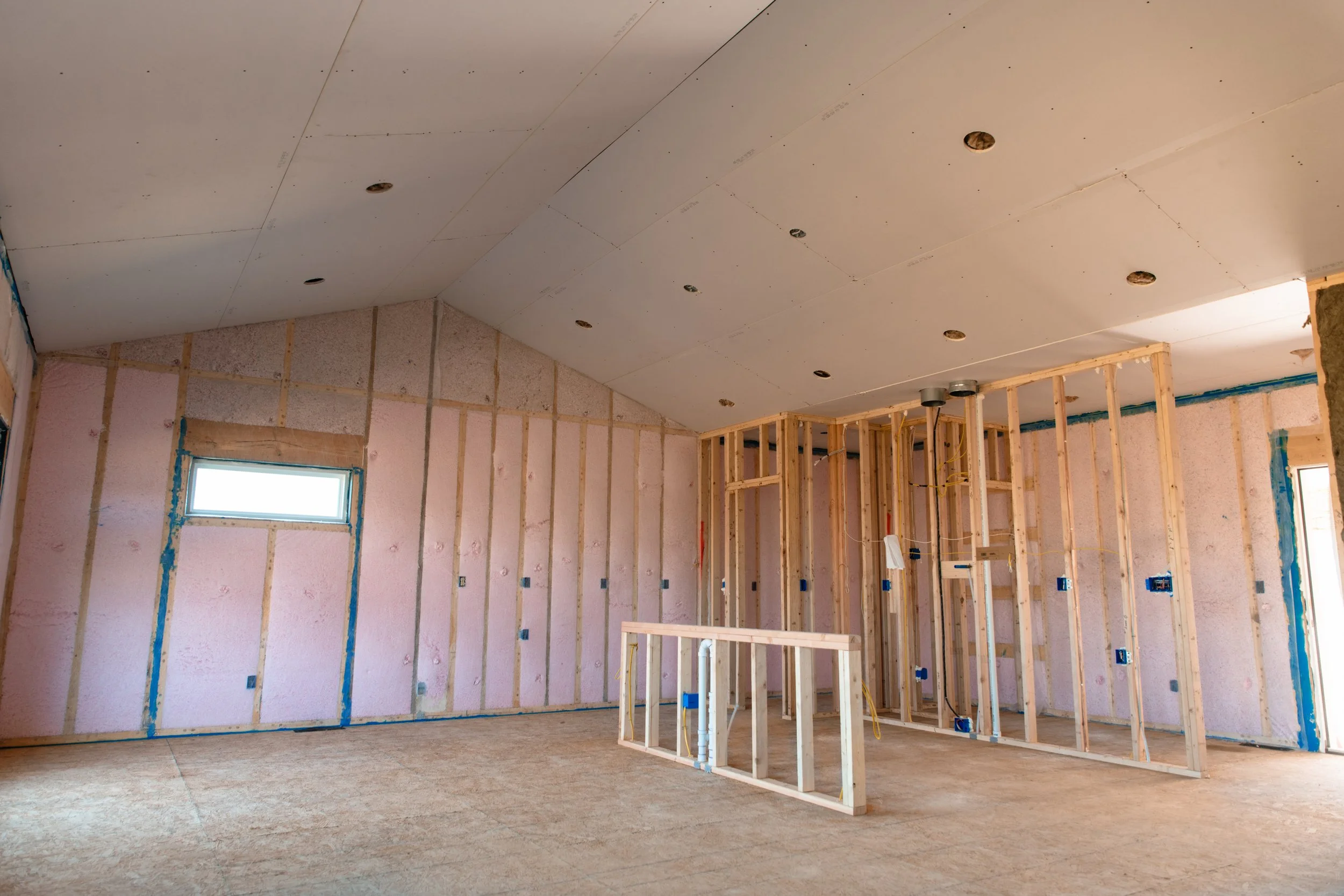
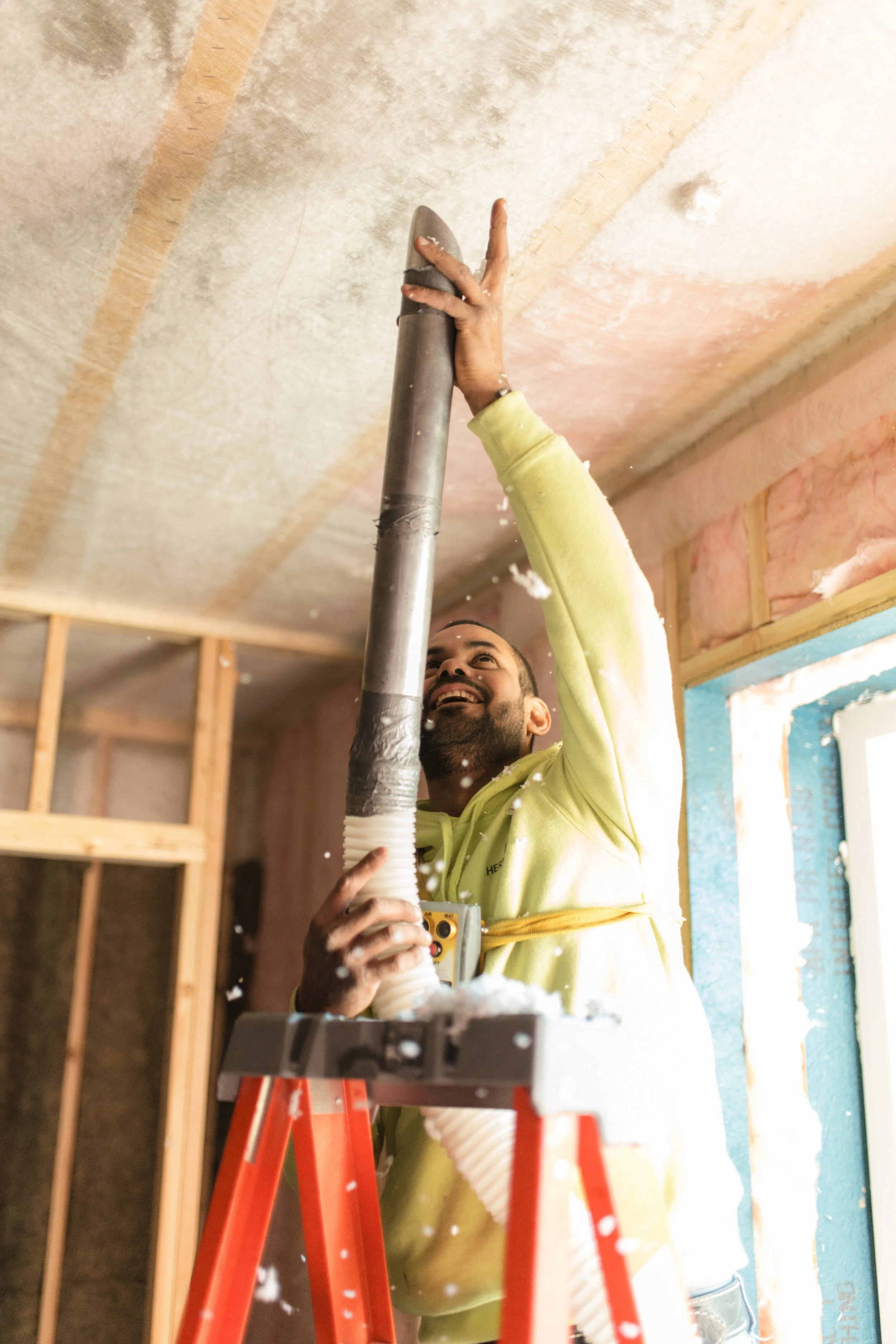
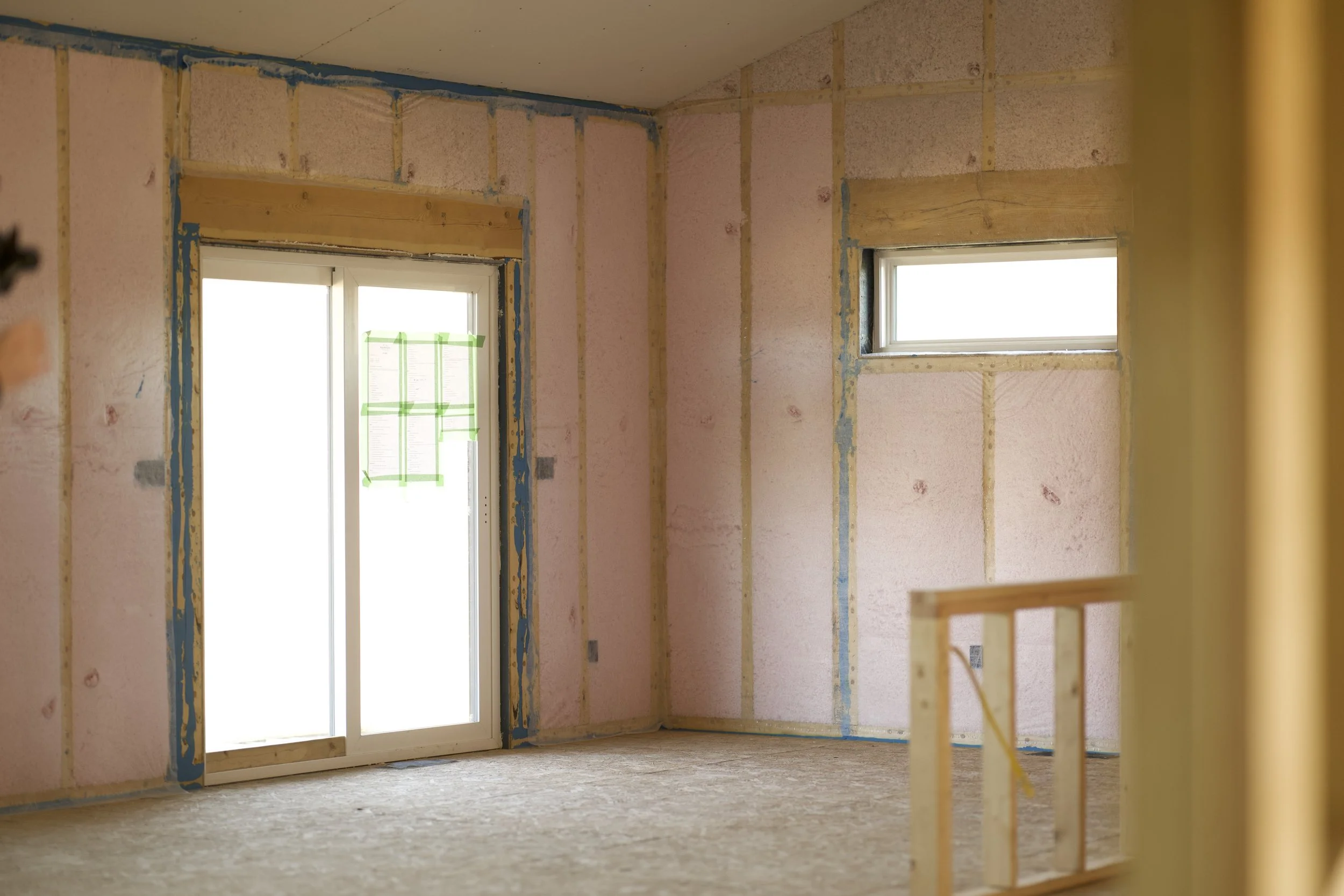
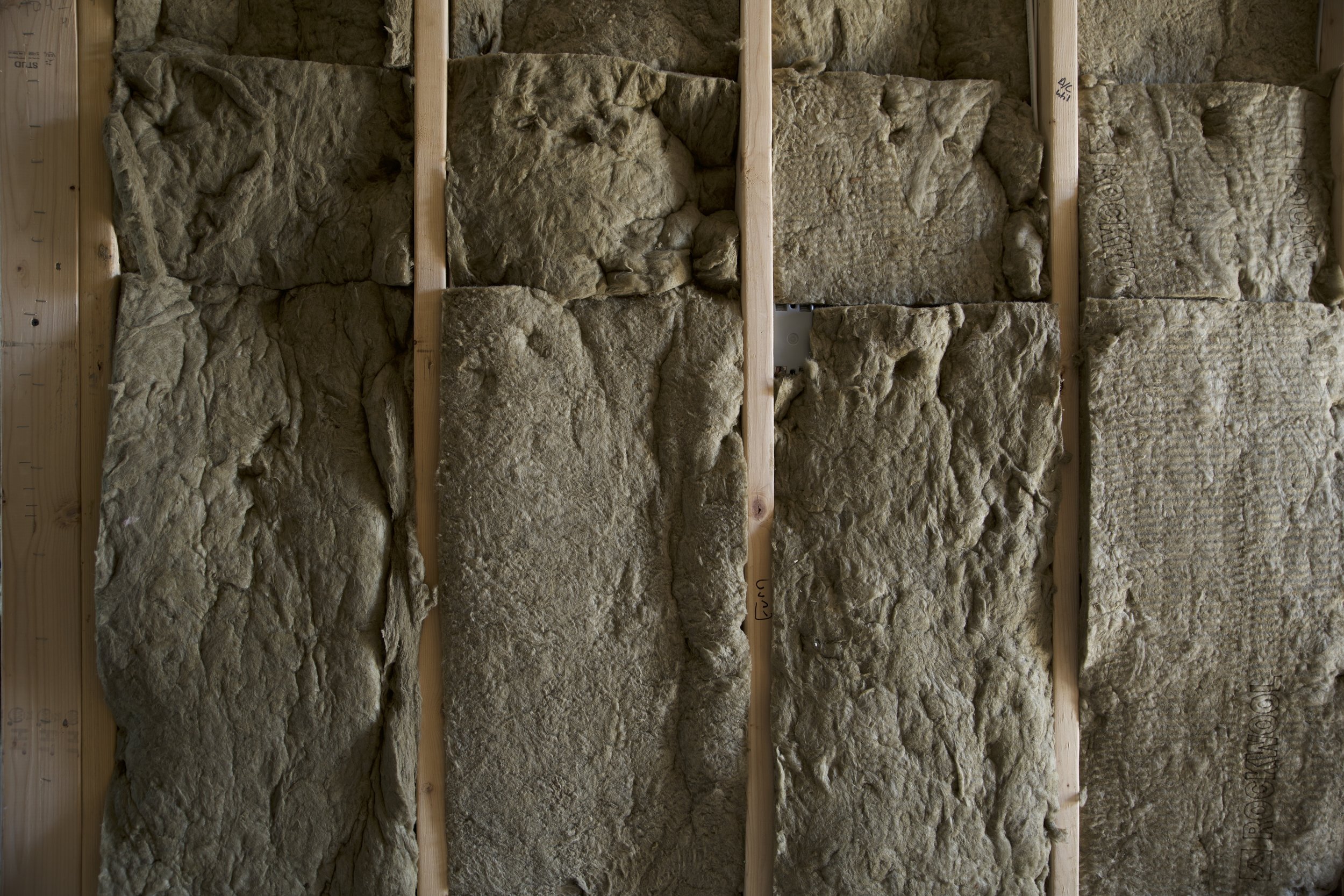
Sound Insulation
All interior walls were sound-insulated with Rockwool mineral wool batts. The entire floor system between the main floor and basement (with the small exceptions of the mechanical rooms) was filled with net & blow fiberglass insulation.
Sound insulation was an important consideration for homeowner Jacob Heffernen, as his growing family requires spaces where they can share in life together and spaces where they can be quietly on their own. If you’d like to learn more about sound insulation, check out our blog post.
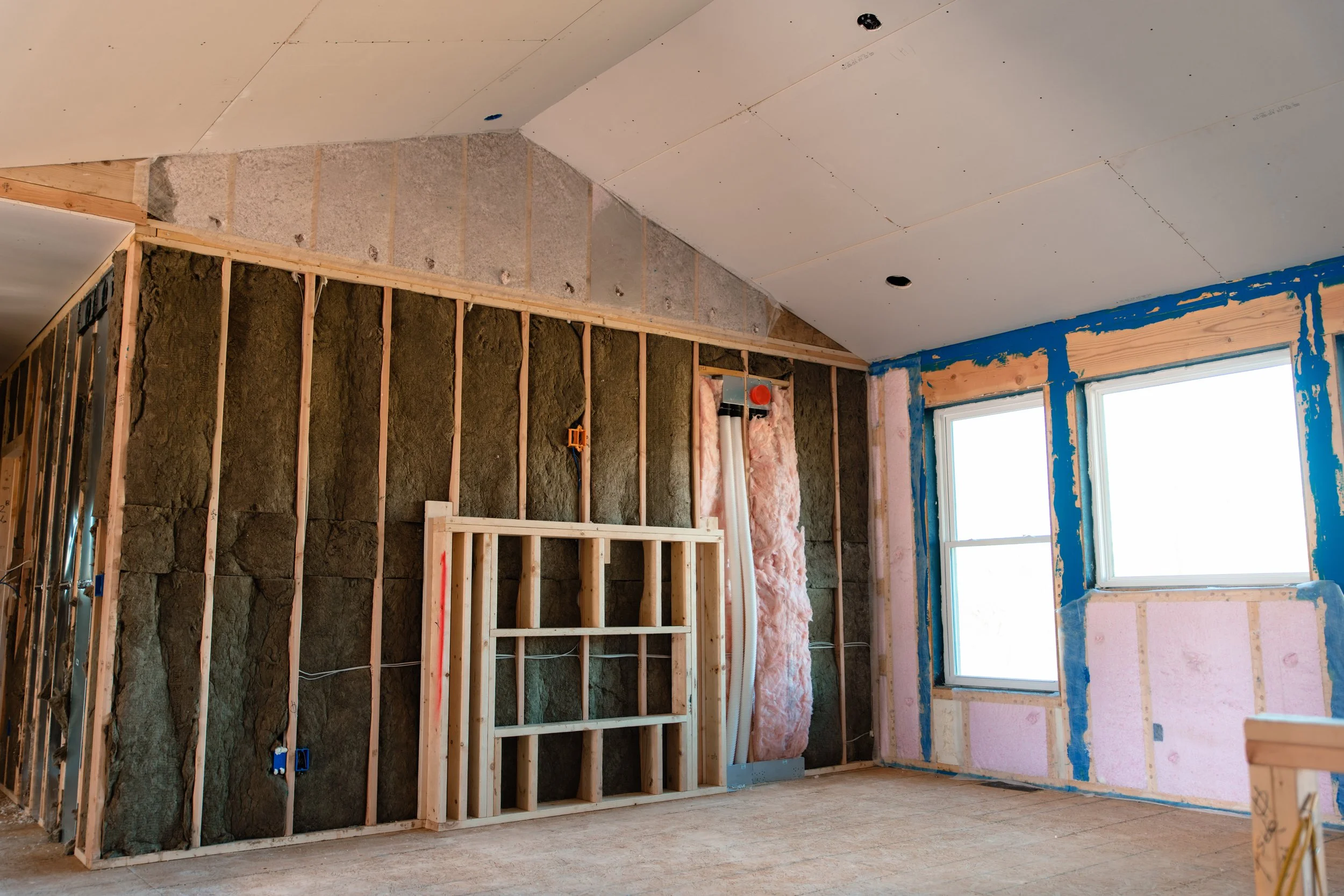
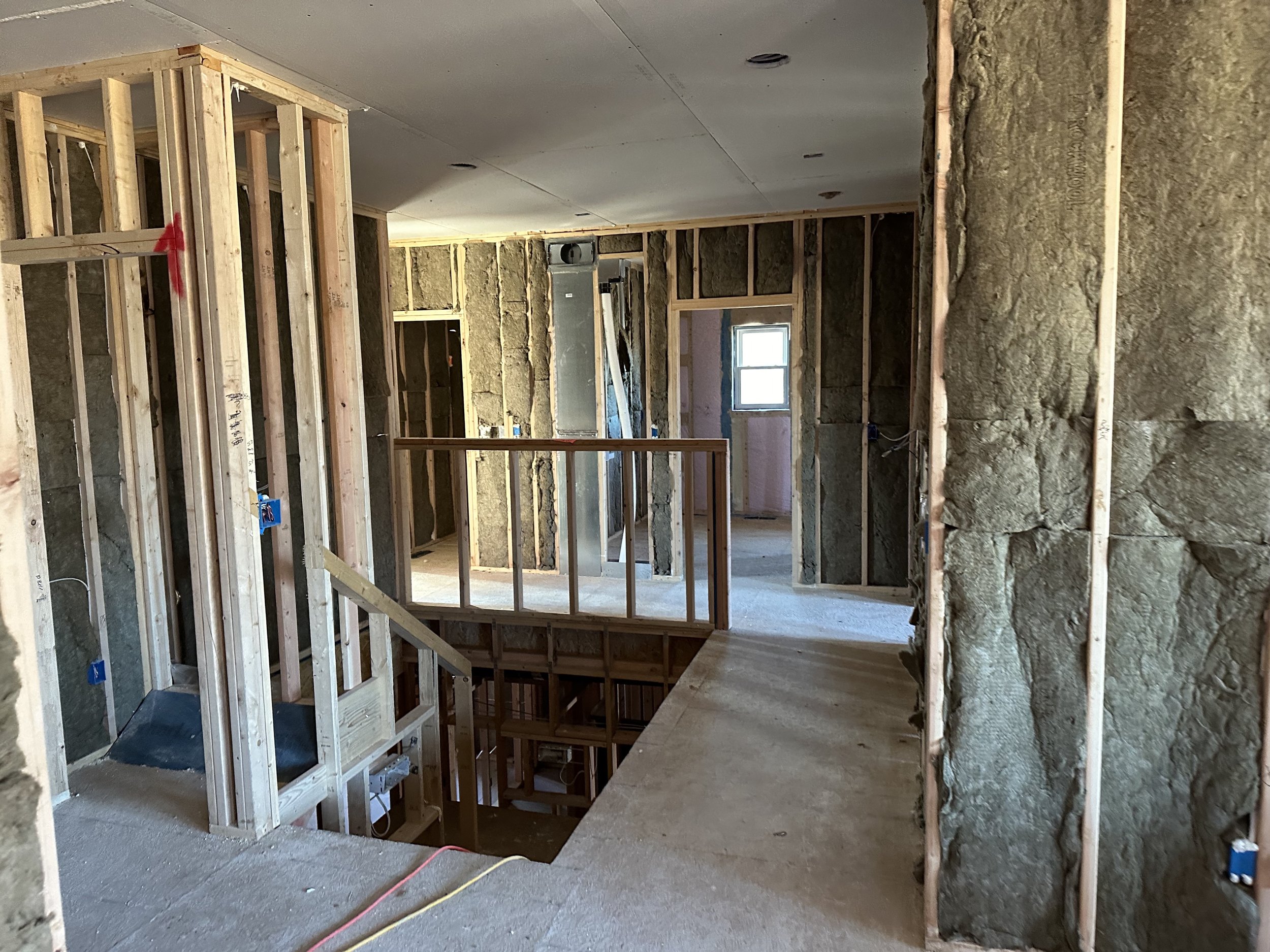
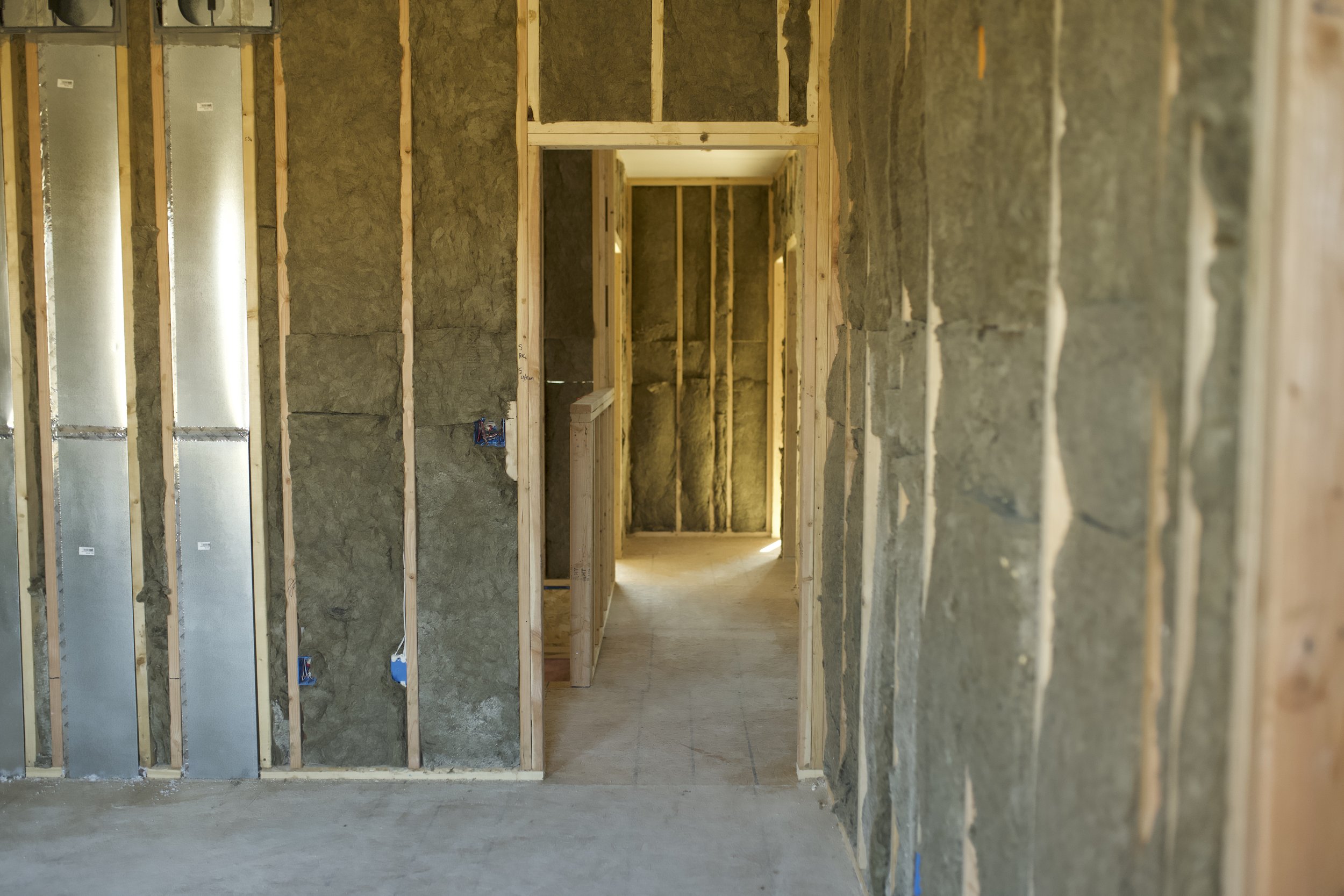
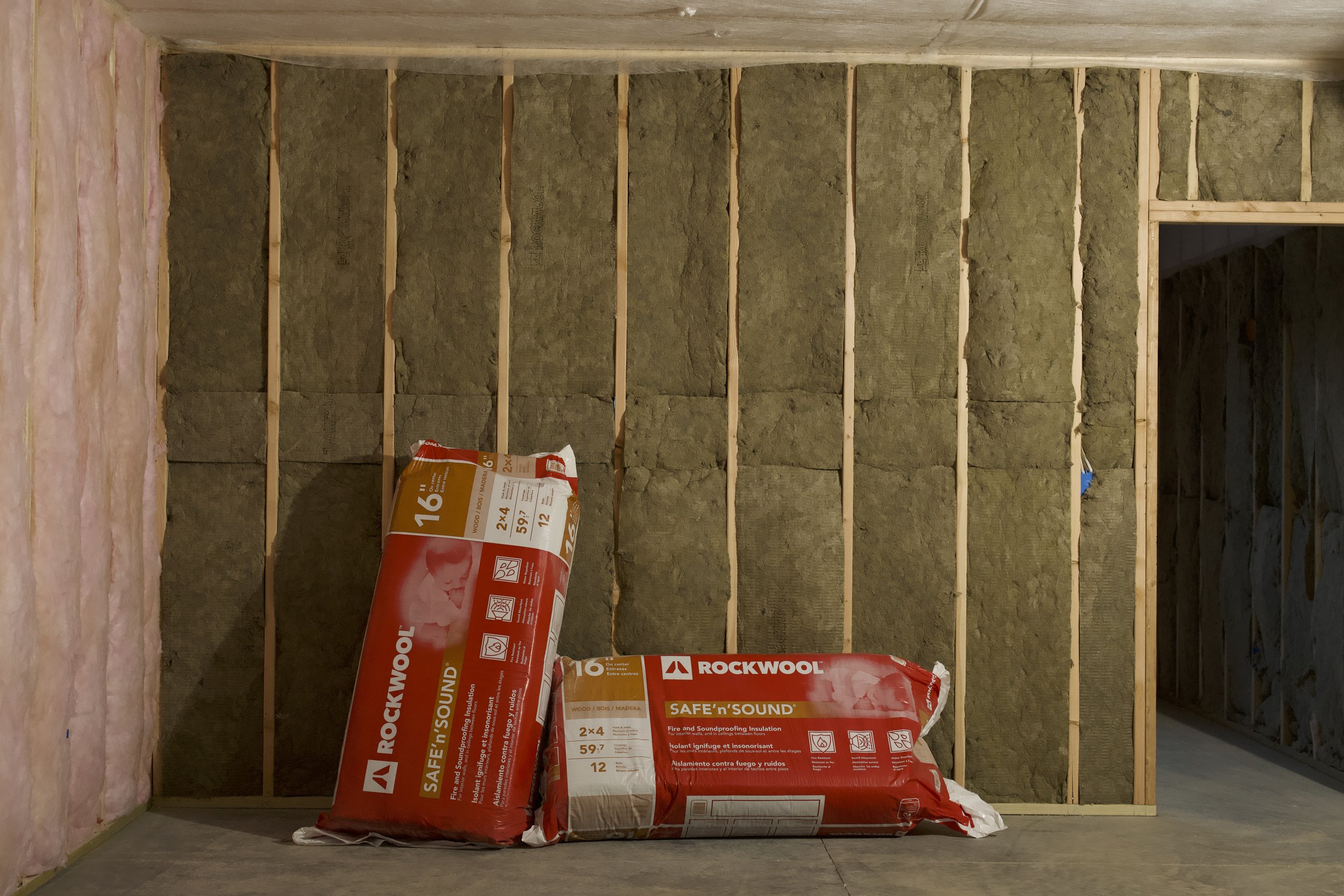
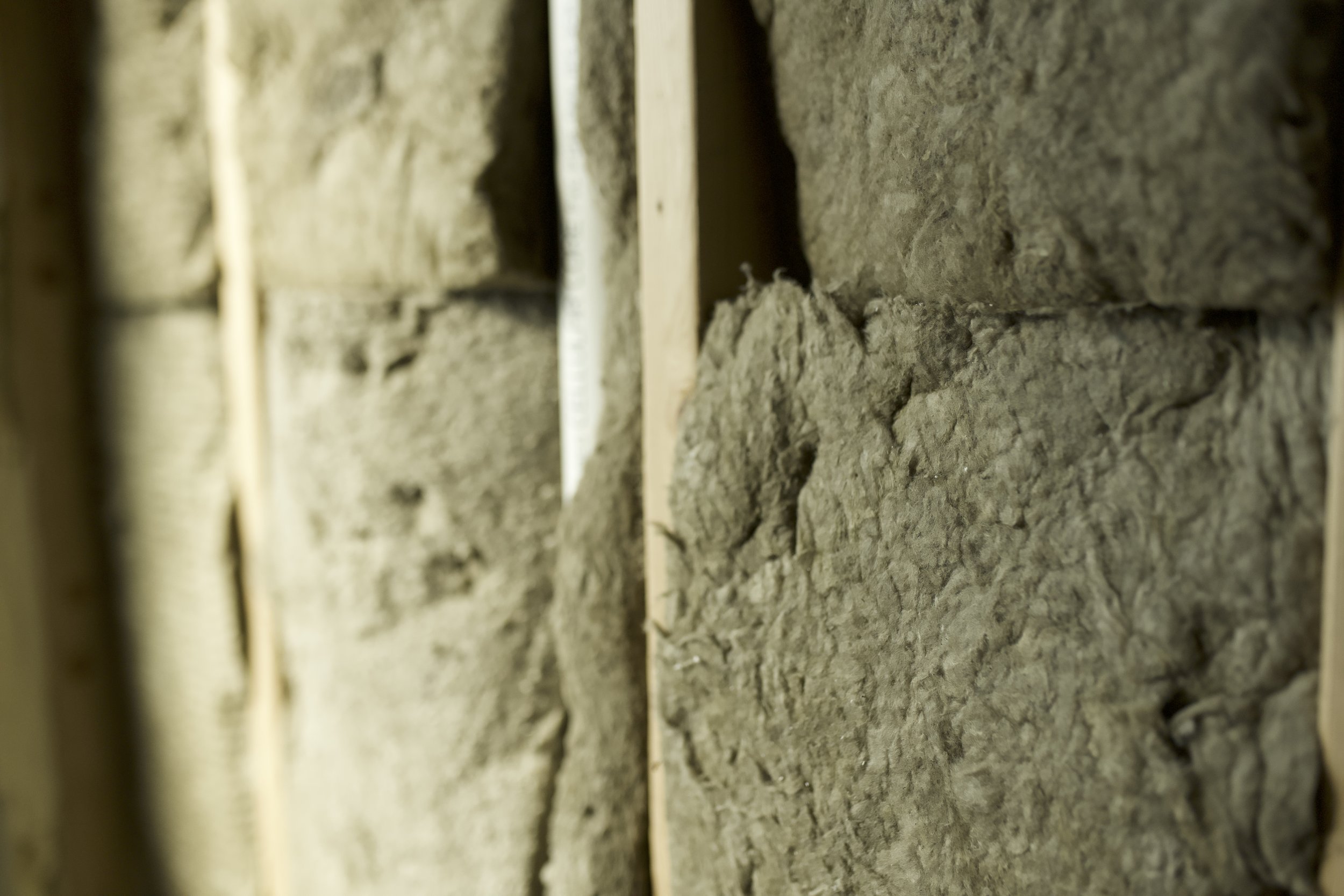
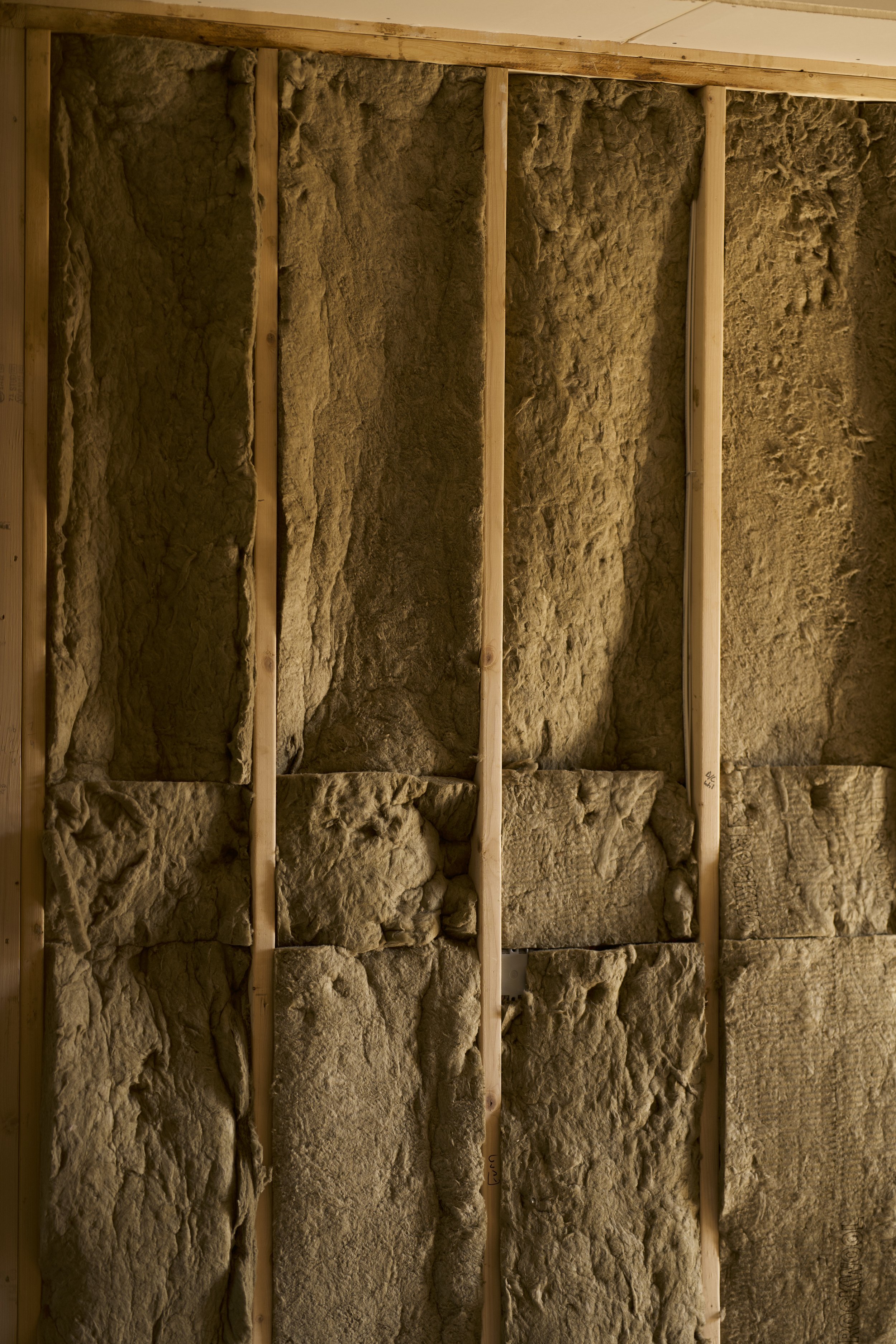
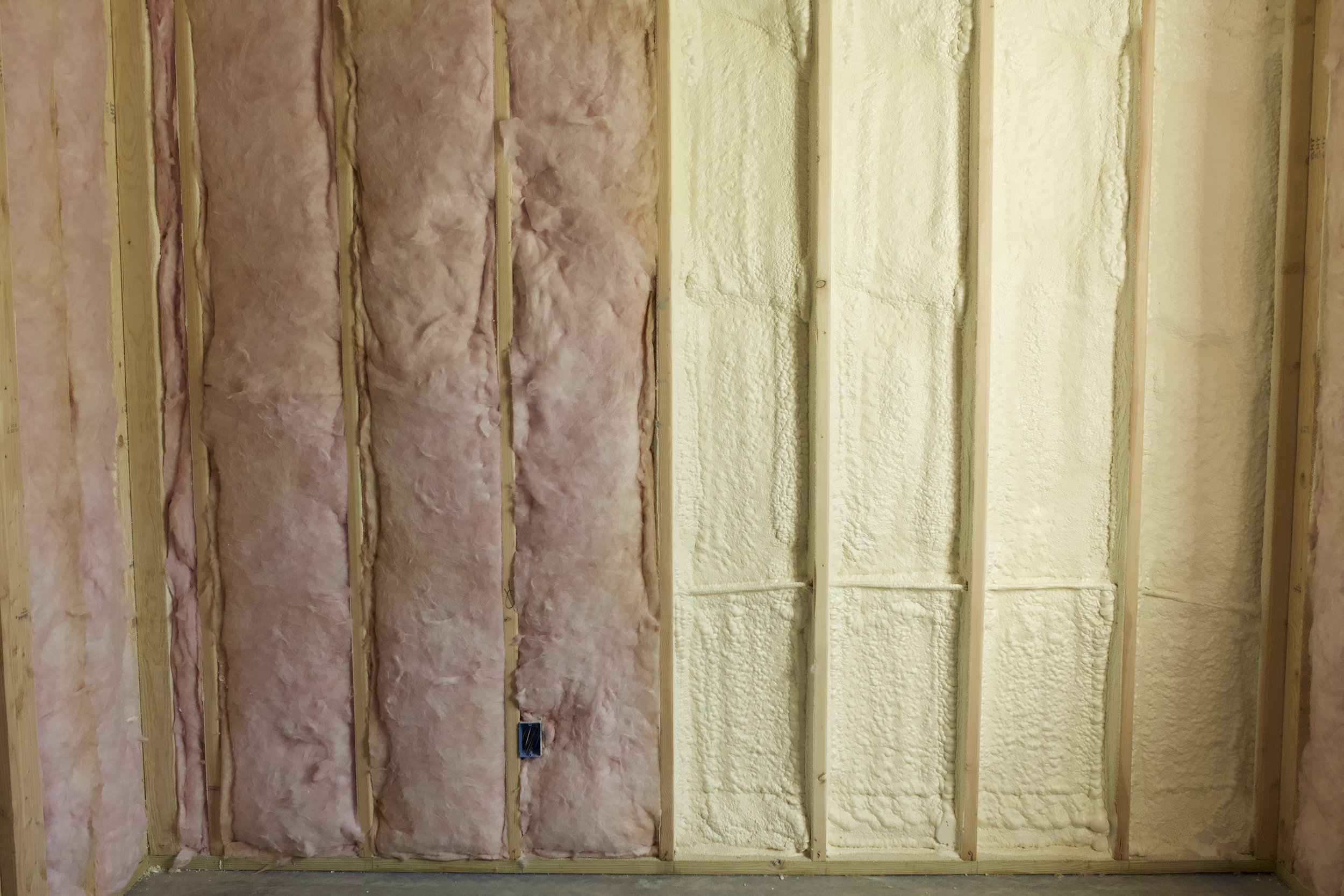
Hybrid Insulation System
For all basement exterior walls, fiberglass was installed over closed cell spray foam. Why? To get the best of both worlds- the unparalleled thermal/air barrier of spray foam and the budget-friendly nature of fiberglass.
The thermal barrier rating of the spray foam is R-14. On top of that, we get R-11 from the fiberglass batts. However, the total R-Value is about R-23 due to slight batt compression.
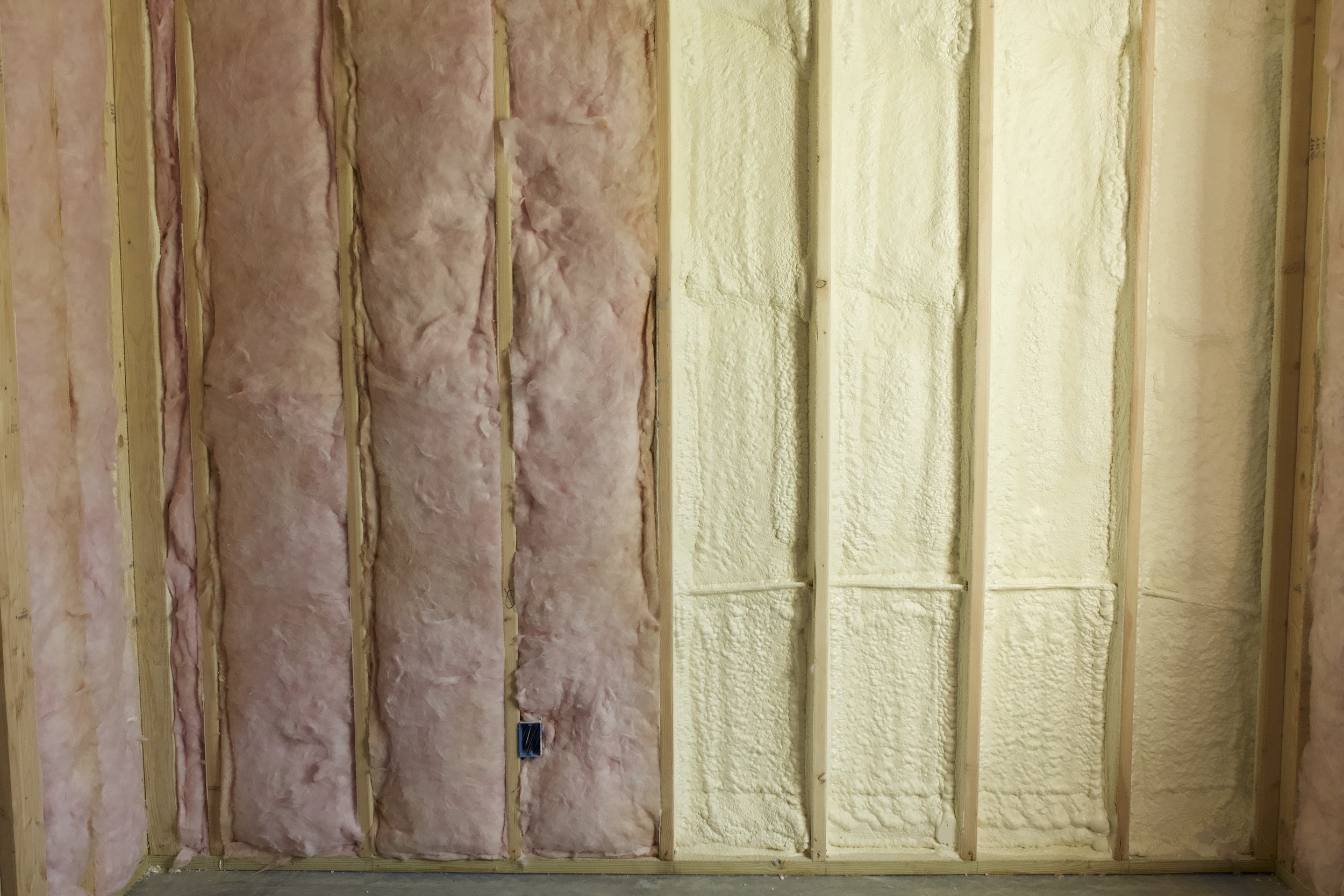
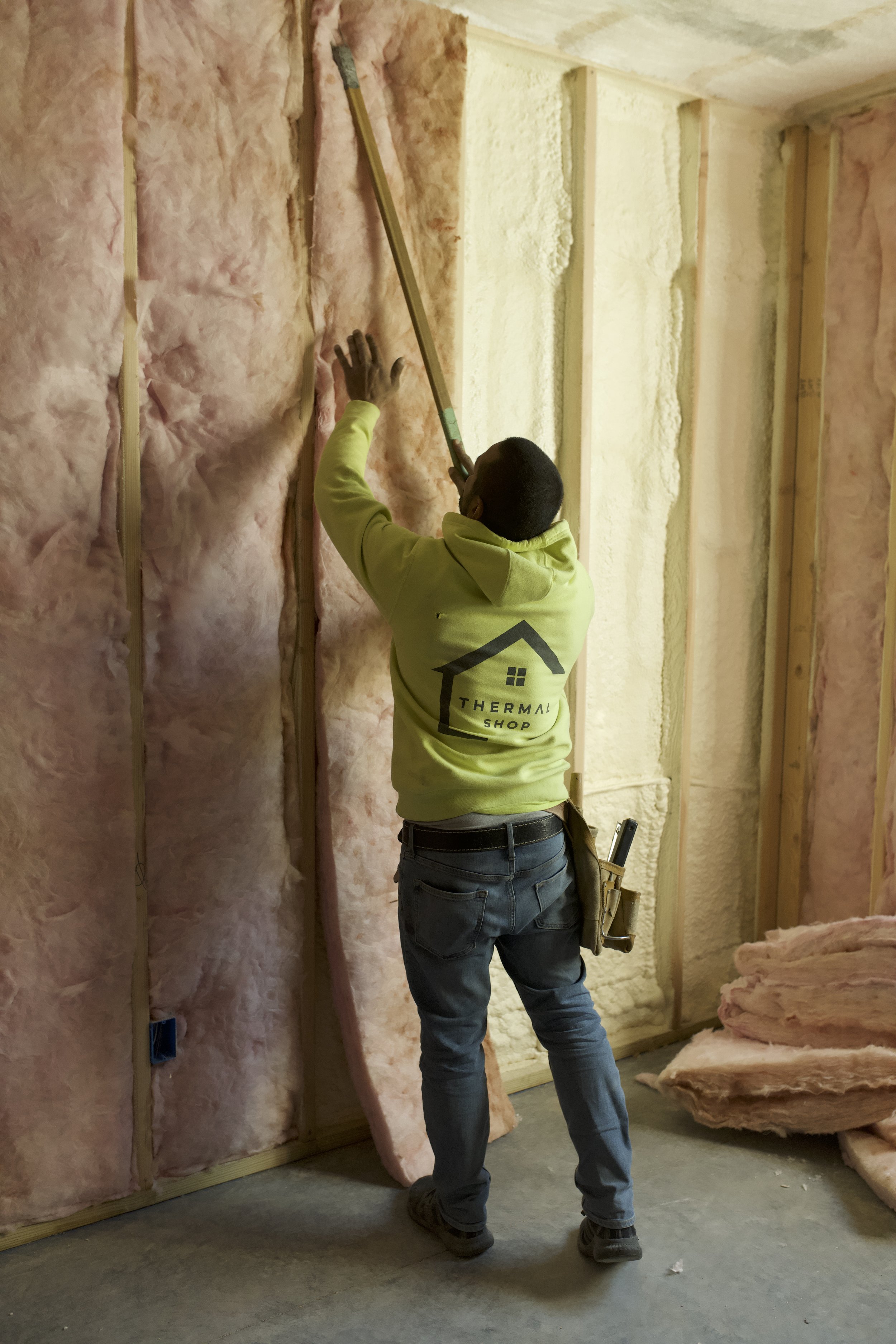
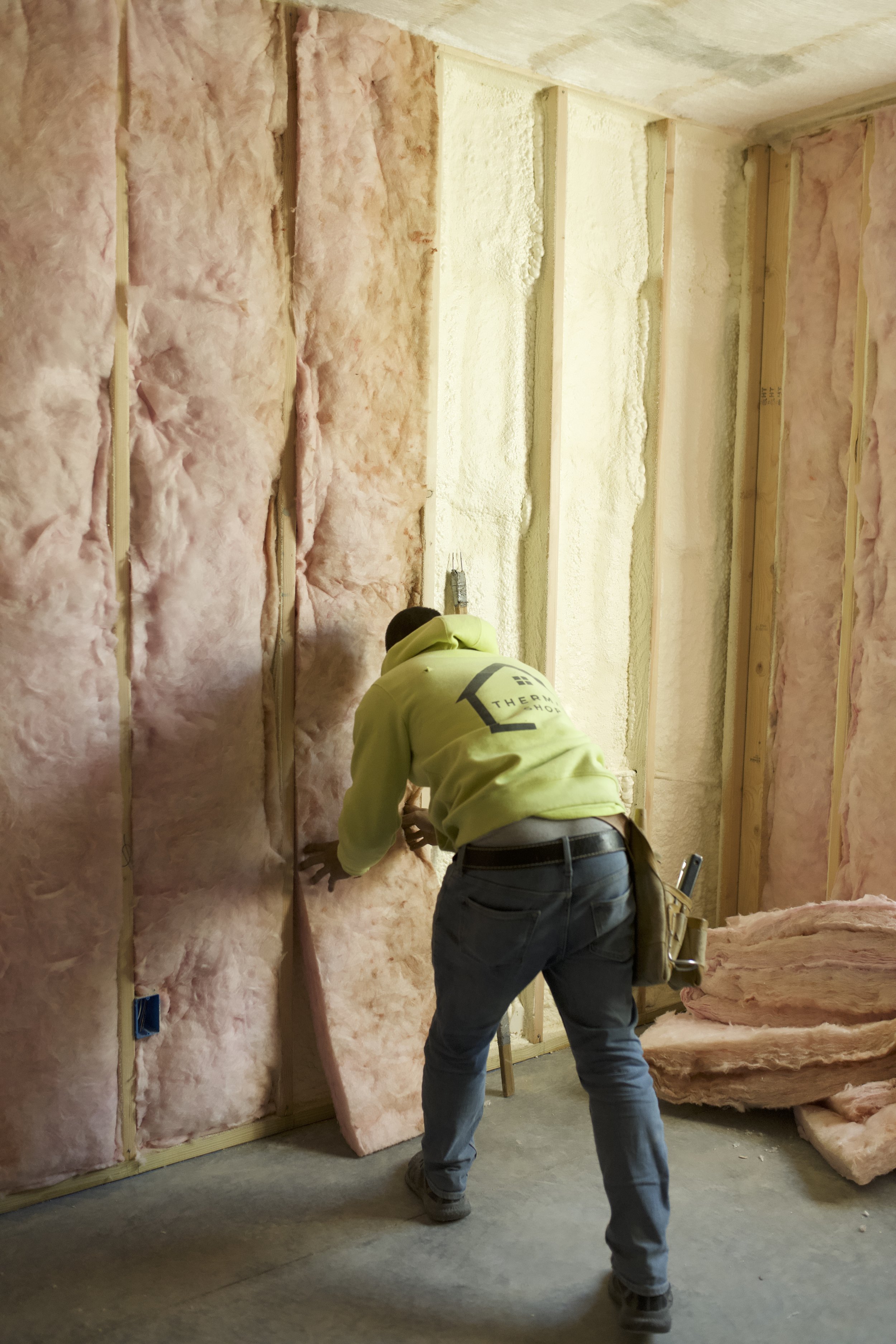
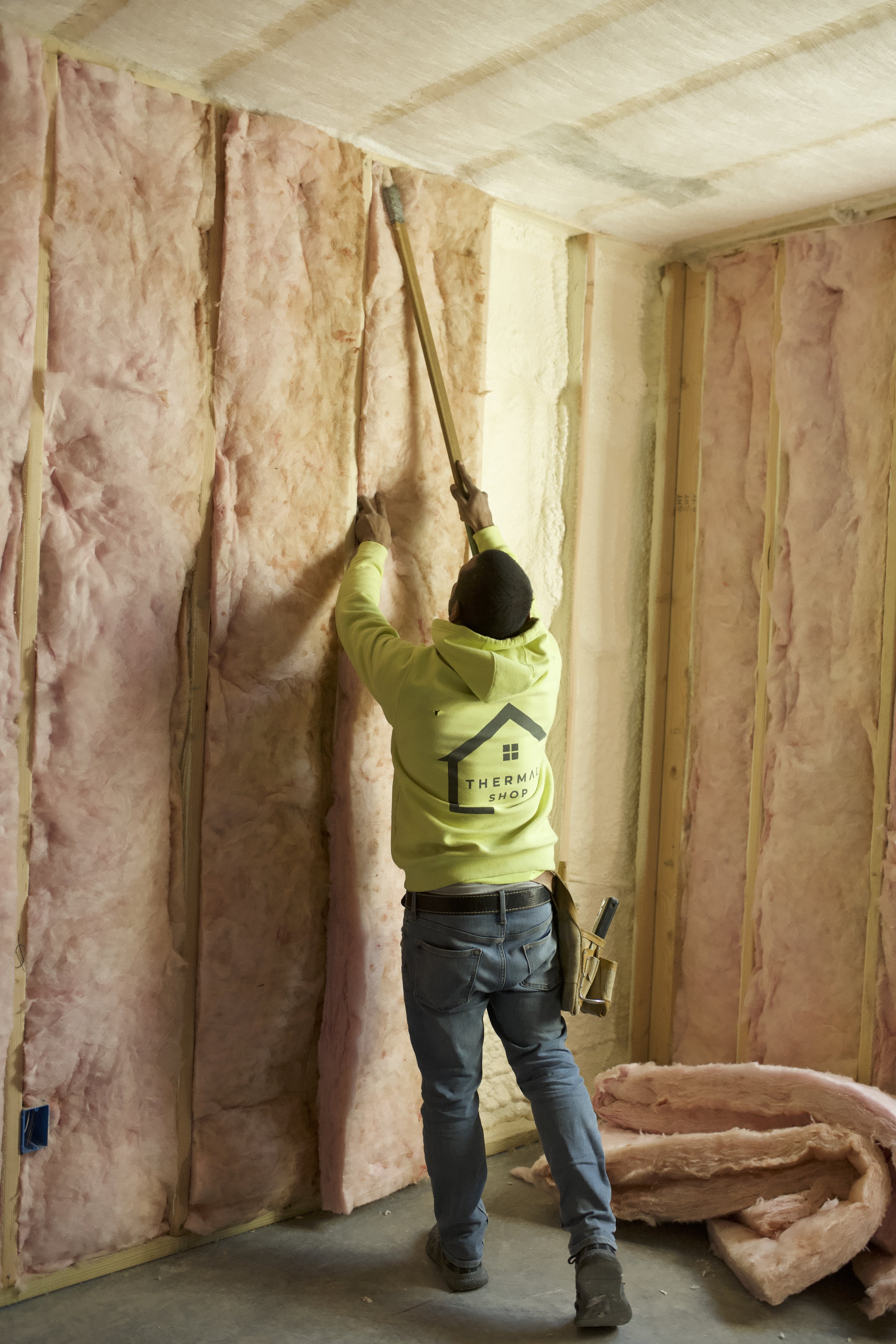
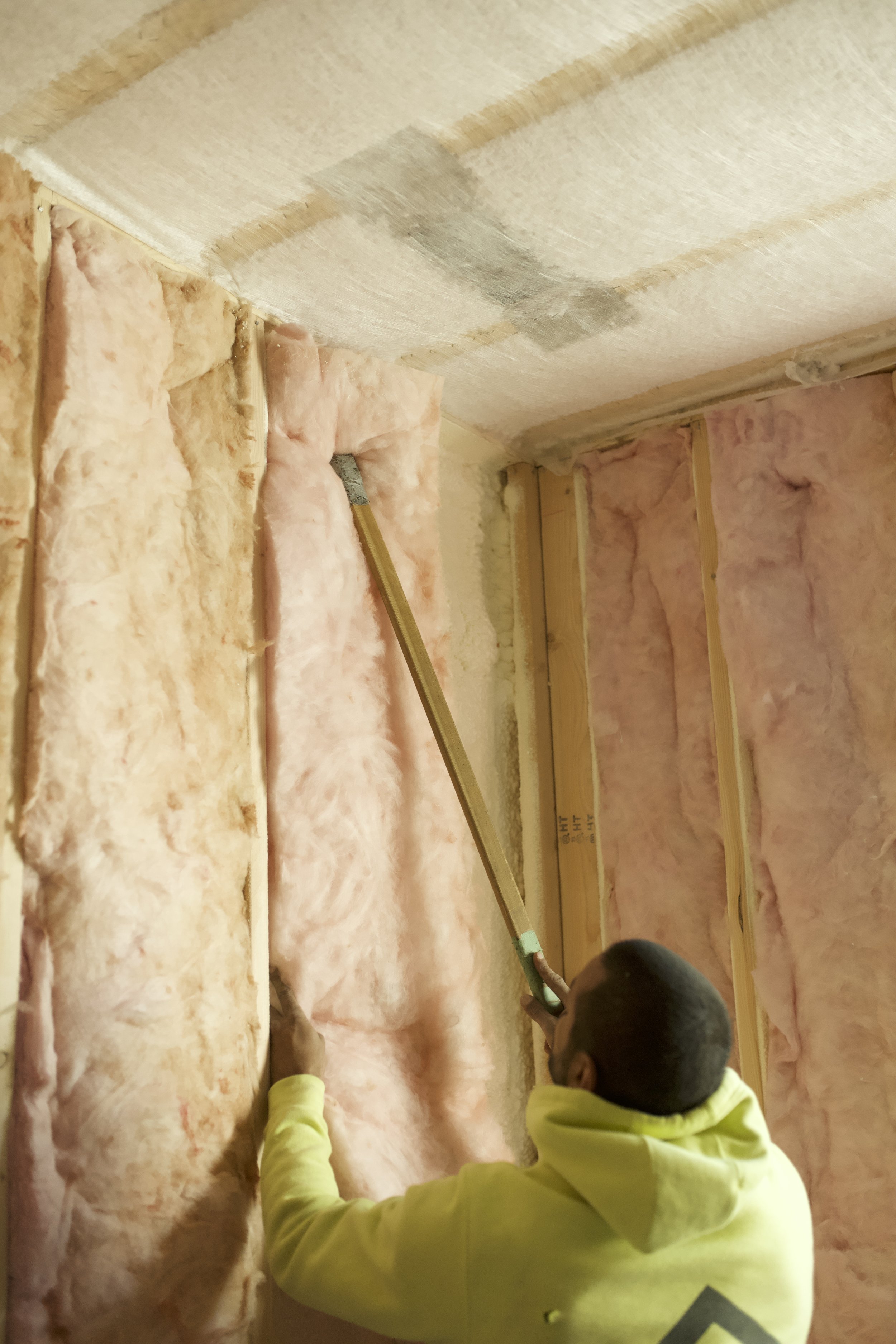
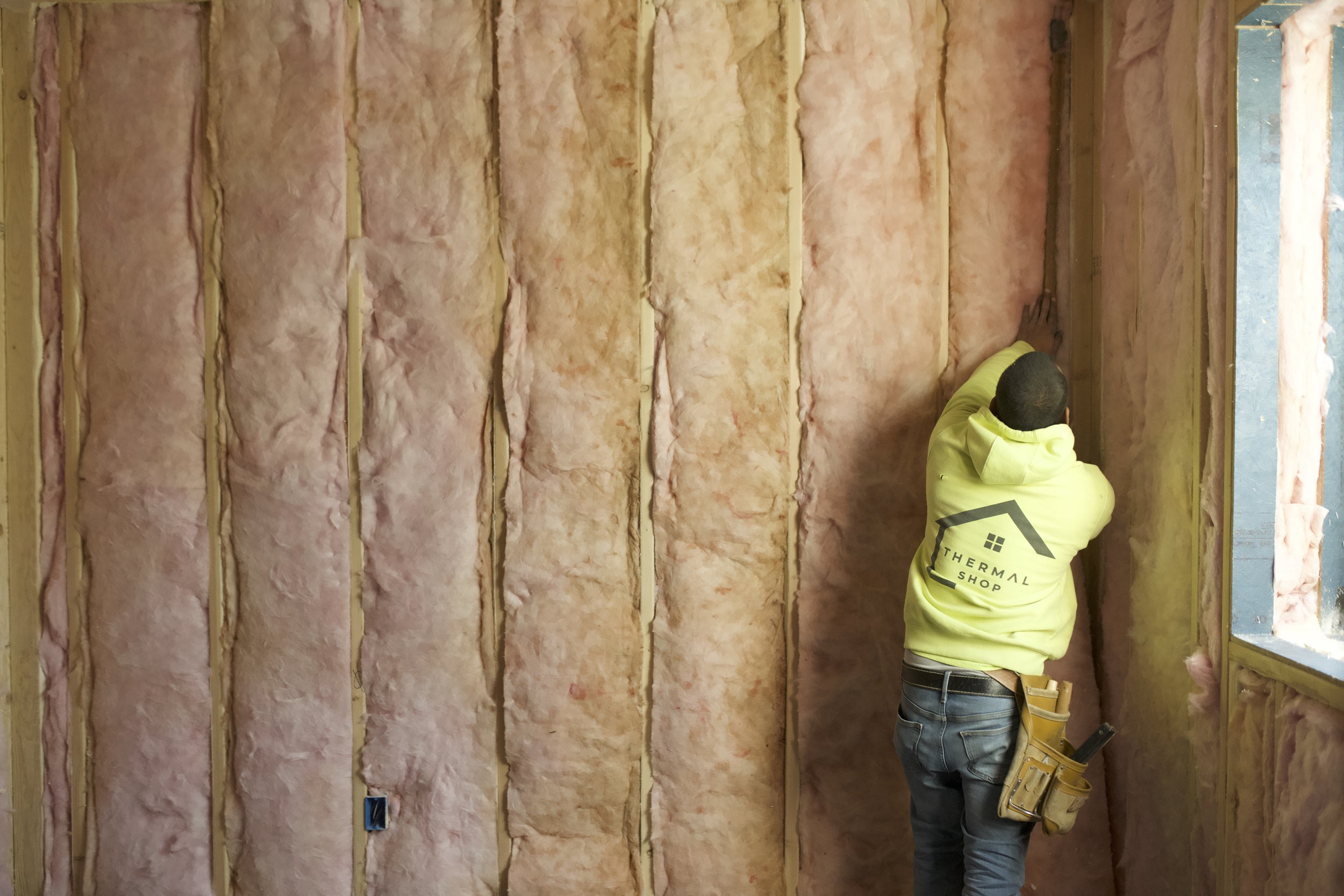

Attic
Timber Creek’s house attic was prepped by applying spray foam around all attic penetrations, top plates, and air chutes. Then, cellulose insulation was blown-in at a thermal ratings of R-60.
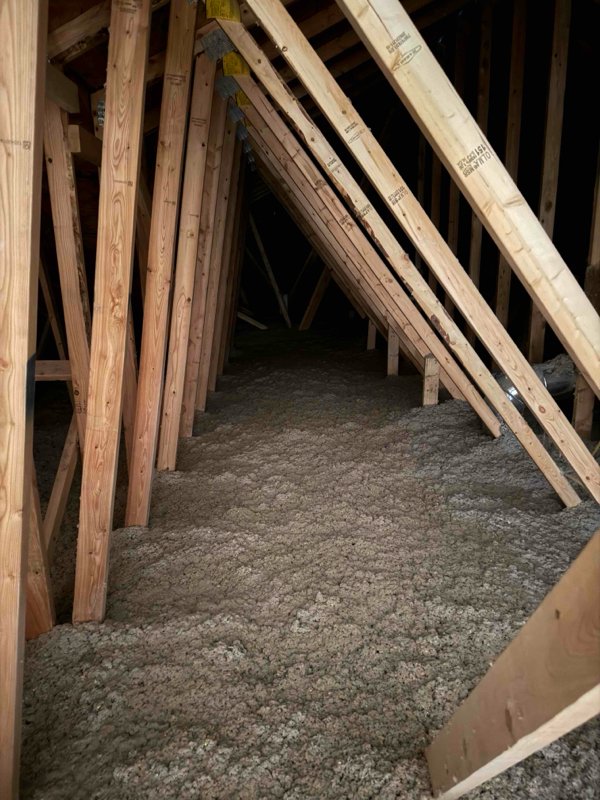
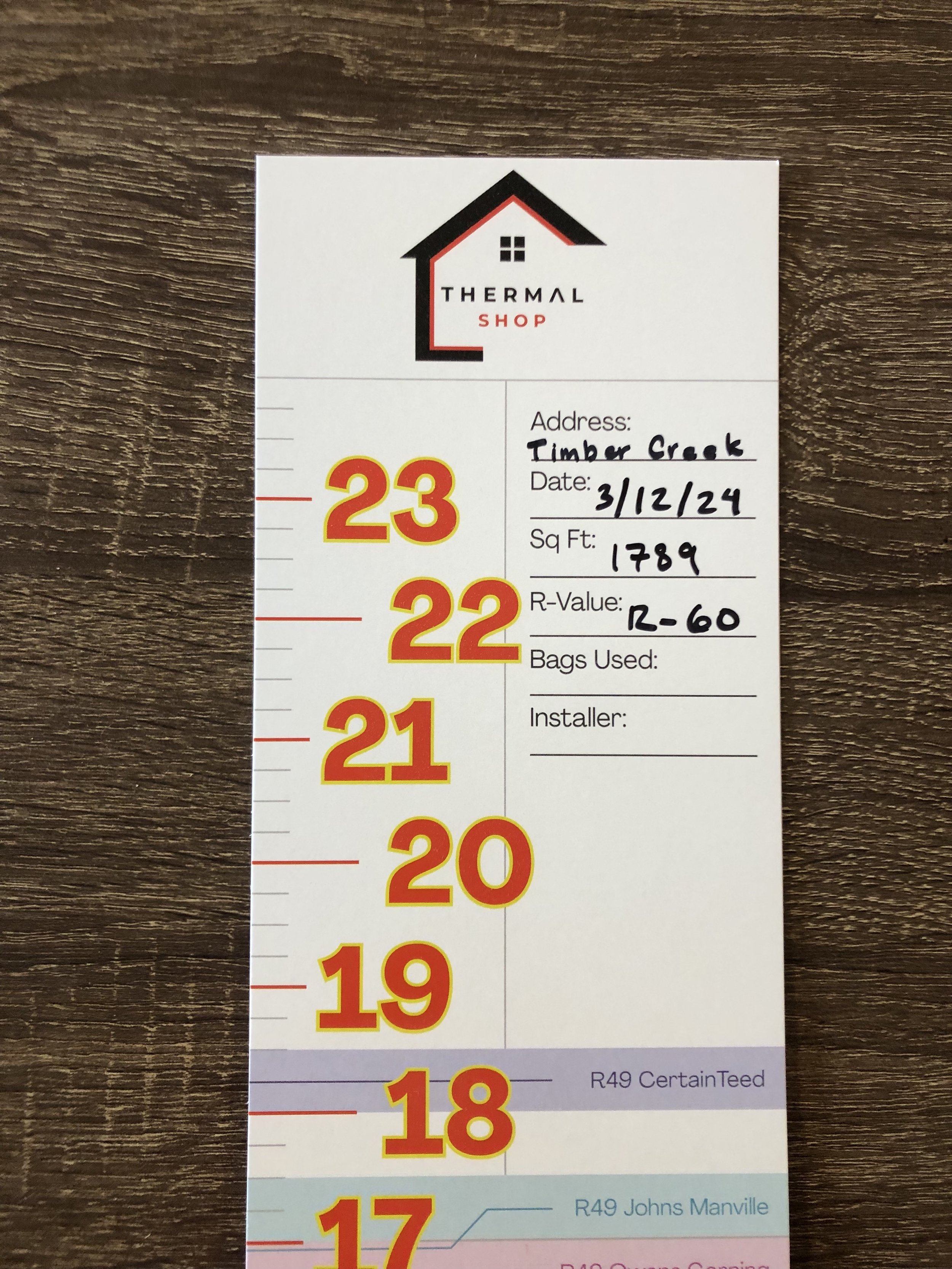

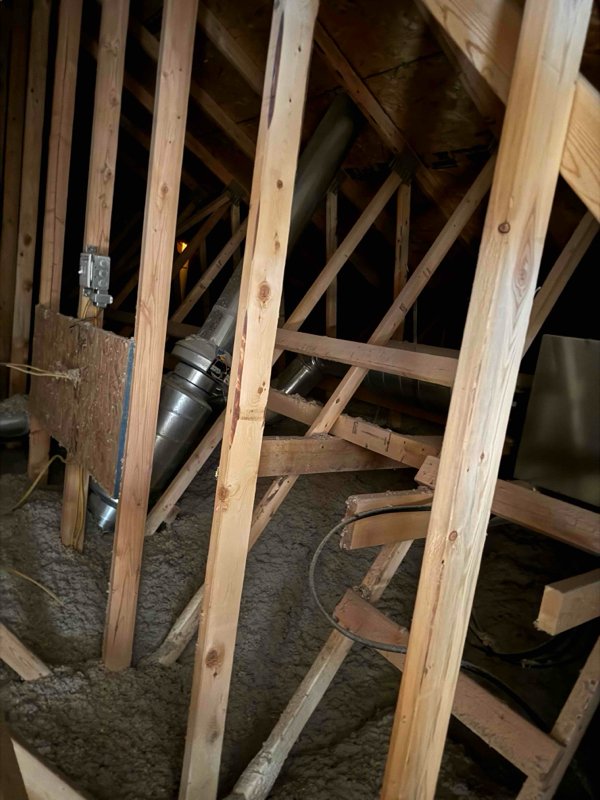
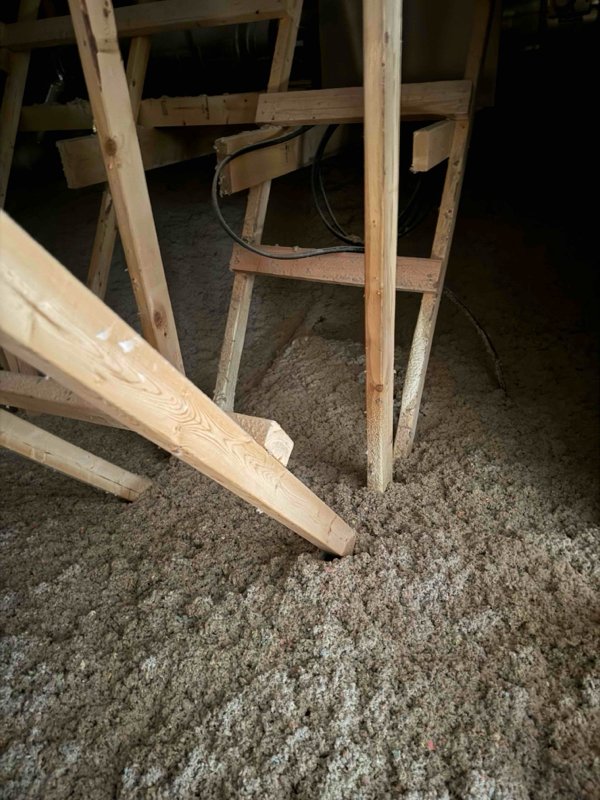
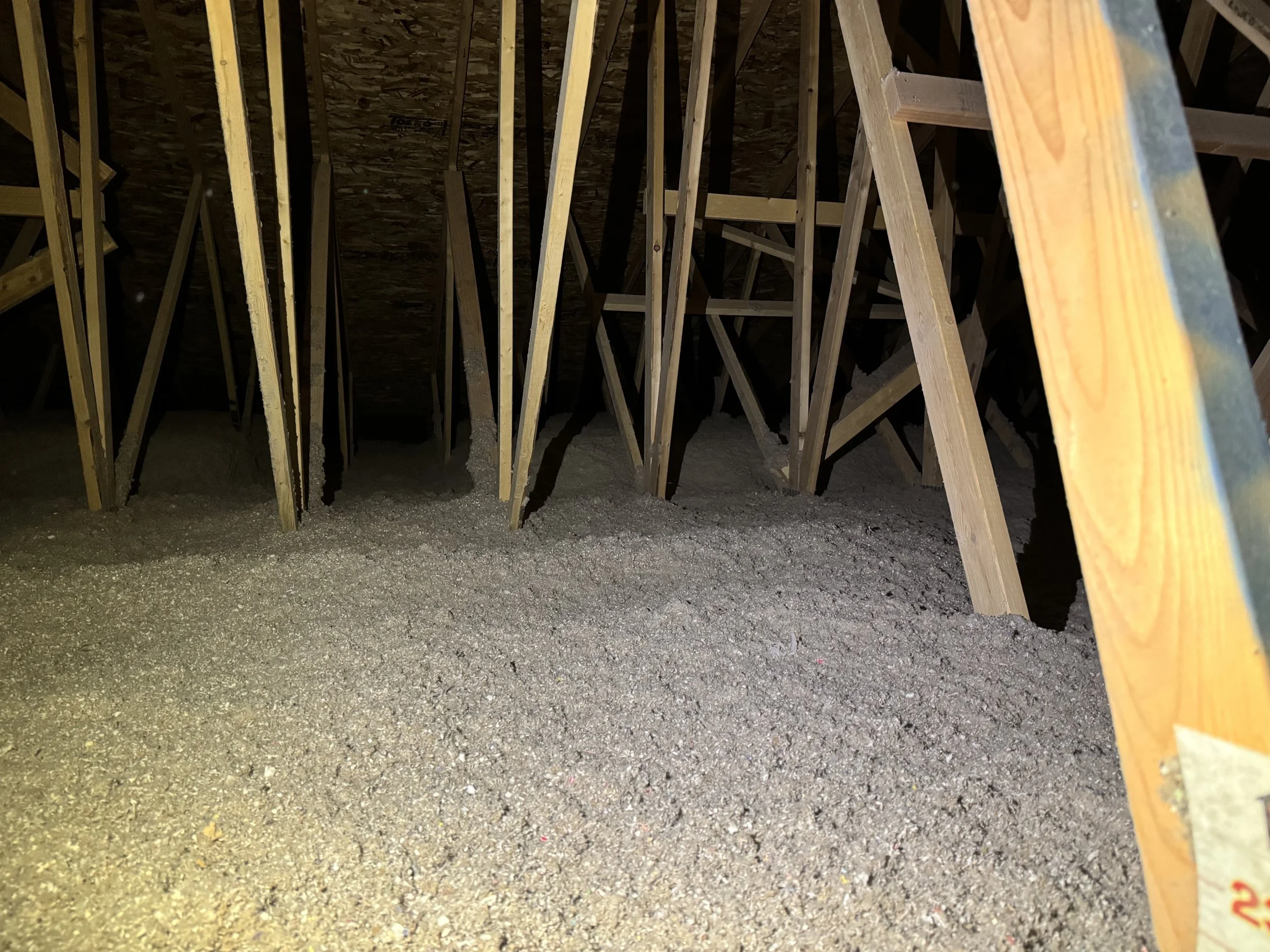
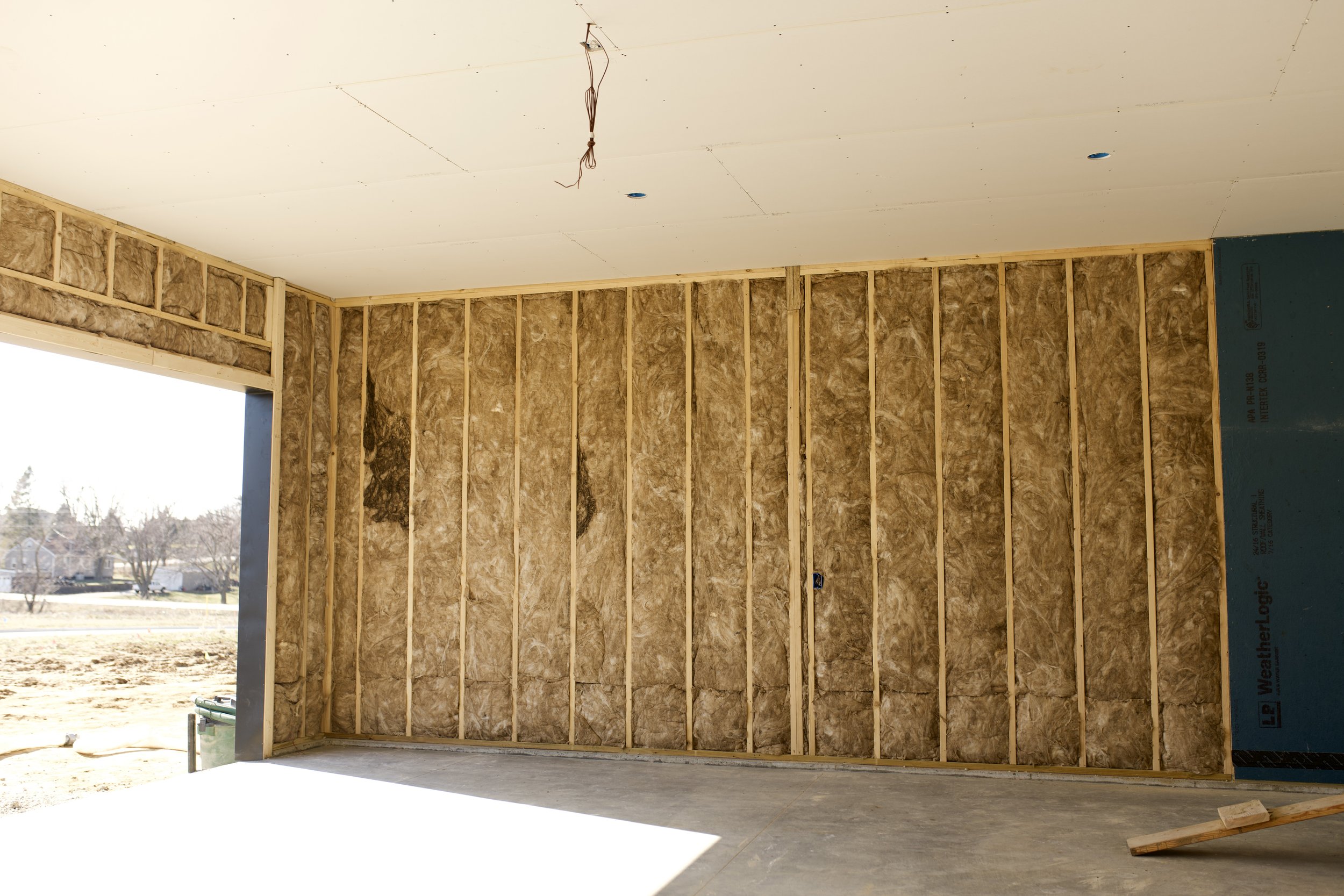
Garage
Timber Creek’s garage received several upgrades compared to the average home. First, the garage attic was insulated at an R-49 with blown cellulose insulation. Second, the 2x6 exterior walls were insulated at an R-21 with batts.
Timber Creek’s garage was insulated to the same standard as a new home because the garage will be conditioned year-round with a high efficiency mini-split.
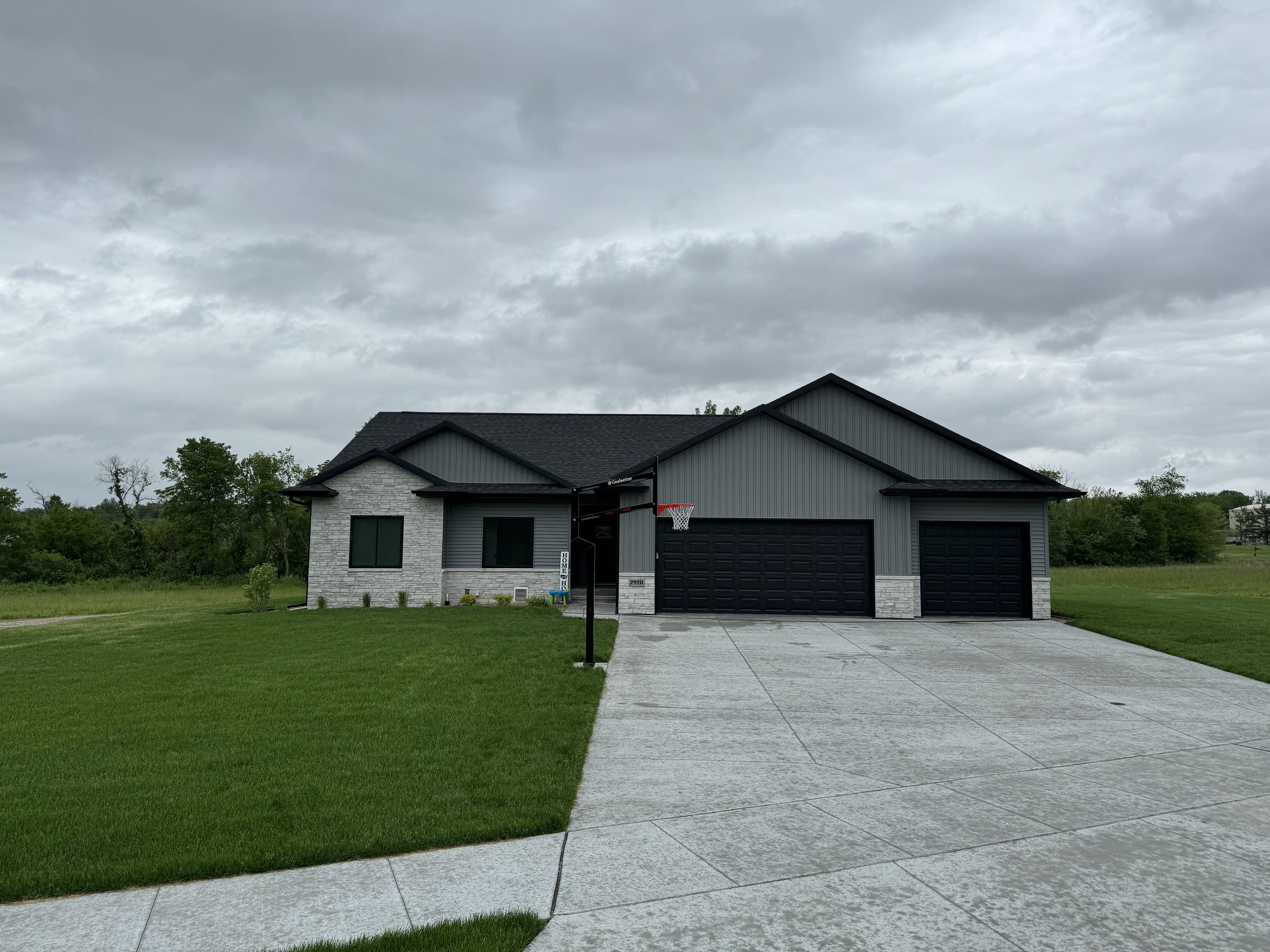
Air Leakage/ HERS Testing
With so much extra effort gone into the insulation and air-sealing of Timber Creek, it may come as no surprise that it passed the blower door test with flying colors, coming in at .56 ACH50, beating the air-leakage testing requirements of a passive home.
Timber Creek also received an impressive HERS score of 36. Thermal Shop’s sister company- Energy Ratings Group- has done code compliance testing for over 1,000 units. This is the lowest scoring unit they’ve ever tested among ones that don’t have renewables.
HERS (Home Energy Rating System) is a nationally recognized method for evaluating the energy performance of a home. The HERS Index is a scale ranging from 1 to 150 with the average 2006 home testing in at 100. The lower score, the more energy efficient the home.